Nitrogen-increasing method for molten steel of ultra-low carbon enamel steel
An enamelled steel, ultra-low carbon technology, applied in the field of iron and steel metallurgy, can solve the unsolved problems such as the matching of nitrogen increasing operation time, refining cycle and continuous casting rhythm.
- Summary
- Abstract
- Description
- Claims
- Application Information
AI Technical Summary
Problems solved by technology
Method used
Image
Examples
Embodiment approach 1
[0020] Such as figure 1 as shown, figure 1 It is a schematic flowchart of a method for increasing nitrogen in molten steel of ultra-low carbon enamel steel provided in Embodiment 1 of the present invention.
[0021] A method for increasing nitrogen in ultra-low carbon enamel molten steel provided by the invention, comprising
[0022] Step S10: transfer the molten iron to the decarburization furnace for smelting. During the decarburization period, use nitrogen as the lifting gas for decarburization and control the flow rate of the lifting gas at 150-170Nm 3 / h, at the same time control the vacuum system pumping, so that the vacuum degree of the decarburization furnace is not greater than 100Pa. In this embodiment, after the molten iron is transferred to the decarburization furnace, the decarburization furnace is firstly subjected to the operation of temperature measurement and oxygen determination, and the natural decarburization process or forced oxygen blowing is determined...
Embodiment approach 2
[0033] The technical solution of the present invention will be further described below through 6 smelting examples of ultra-low carbon enamel steel molten steel smelting.
[0034] The control of the vacuum system during decarburization is: use the 2-stage pump of the vacuum pump to pump air, so that the vacuum degree of the decarburization furnace is below 100Pa, and the decarburization is performed for 5-8 minutes. At this time, the vacuum degree of the decarburization furnace is not greater than 1kPa. At the same time, input lifting gas nitrogen to the decarburization furnace, and the lifting gas flow rate is 150-170Nm 3 / h. During the 5-8 minutes of decarburization, gradually increase the gas flow rate to 210-230Nm 3 / h between. The whole decarburization time is about 15-18min, maintain this boost gas flow rate 210-230Nm 3 / h level to the end of decarburization, at this time the carbon content in the molten steel in the decarburization furnace is not more than 20ppm.
...
PUM
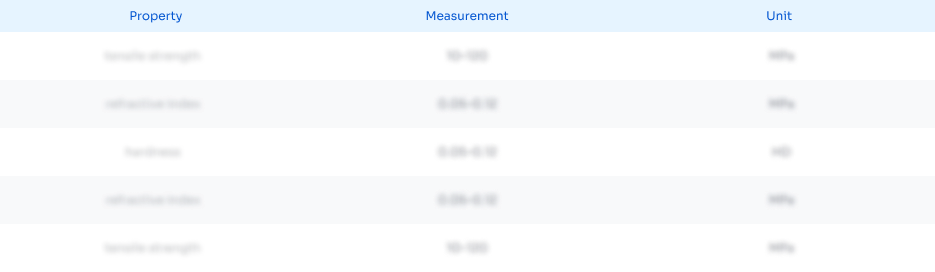
Abstract
Description
Claims
Application Information

- R&D
- Intellectual Property
- Life Sciences
- Materials
- Tech Scout
- Unparalleled Data Quality
- Higher Quality Content
- 60% Fewer Hallucinations
Browse by: Latest US Patents, China's latest patents, Technical Efficacy Thesaurus, Application Domain, Technology Topic, Popular Technical Reports.
© 2025 PatSnap. All rights reserved.Legal|Privacy policy|Modern Slavery Act Transparency Statement|Sitemap|About US| Contact US: help@patsnap.com