Porous submersed nozzle for pouring blooms
An immersed, blooming technology, used in casting melt containers, metal processing equipment, casting equipment, etc., can solve the problems of melting loss and falling off of the end orifice
- Summary
- Abstract
- Description
- Claims
- Application Information
AI Technical Summary
Problems solved by technology
Method used
Image
Examples
Embodiment Construction
[0022] The technical solutions of the present invention will be further described below in conjunction with the accompanying drawings and embodiments.
[0023] see Figure 5 ~ Figure 6 As shown, the porous submerged nozzle 10 for casting blooms of the present invention includes a nozzle body 11, which is in the shape of a cylindrical tube with a central through hole. The bottom of the end of the body 11 is a closed structure, corresponding to the four walls of the crystallizer. Have a pair of molten steel spit holes 12 arranged up and down on each side respectively, totally eight, and the vertical centerlines of every pair of molten steel spit holes 12 are on the same line. Wherein, the angle a between the upper molten steel spout hole 12 and its horizontal centerline is set at -15° to -45°, and the angle b between the lower molten steel spout hole 12 and its horizontal centerline is set at 15° to 45° . In the same pair of molten steel discharge holes 12, the distance betwee...
PUM
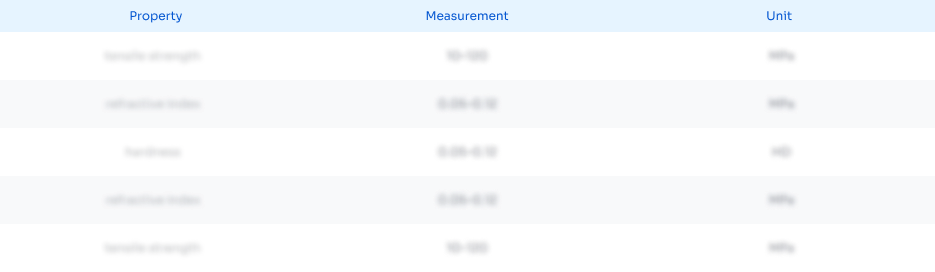
Abstract
Description
Claims
Application Information

- R&D Engineer
- R&D Manager
- IP Professional
- Industry Leading Data Capabilities
- Powerful AI technology
- Patent DNA Extraction
Browse by: Latest US Patents, China's latest patents, Technical Efficacy Thesaurus, Application Domain, Technology Topic, Popular Technical Reports.
© 2024 PatSnap. All rights reserved.Legal|Privacy policy|Modern Slavery Act Transparency Statement|Sitemap|About US| Contact US: help@patsnap.com