Magnetic iron ore concentrating technology
A magnetite and process technology, applied in the field of magnetite selection process, can solve the problems of being unsuitable for the metallurgical industry concentrate policy, energy saving and environmental protection, unsuitable for lean magnetite ore beneficiation, and low iron concentrate grade, etc. The effect of low, improving grade and high recovery rate
- Summary
- Abstract
- Description
- Claims
- Application Information
AI Technical Summary
Problems solved by technology
Method used
Image
Examples
Embodiment 1
[0023] Taking Pingwu iron ore with a grade of 36.84% iron as an example, the iron ore is crushed through a crusher for primary crushing, and the ore discharge particle size is not greater than 200mm. The product after primary crushing enters the jaw crusher again for secondary crushing , the ore discharge particle size is not greater than 40mm, the secondary crushed product and water enter the ball mill for grinding at a mass ratio of 1:1, and the pulverized pulp enters the high-frequency sieve for screening, and the product with a particle size greater than 100 mesh on the sieve is returned The ball mill grinds again; after screening, the qualified (product particle size is not greater than 100 mesh) pulp and water enter the magnetic separation unit with a mass ratio of 1:2 for magnetic separation. The magnetic separation unit consists of three 2500-3000 Gauss magnetic Concentrator structure, the pulp enters the magnetic separator for magnetic separation to obtain rough concen...
Embodiment 2
[0026] Taking the Aba Xiaohe iron ore with a grade of 33.62% iron as an example, the beneficiation process is the same as Example 1, and finally a concentrate with a grade of 64.44% iron is obtained.
[0027] Similarly, the concentrate and the secondary concentrate mixture entering the circulation barrel from the magnetic separation unit and the strong magnetic separator in this embodiment are detected to obtain the grade of the mixture containing 54.49% iron, and the concentrate entering the concentrate overflow pipe is detected The iron content of the concentrate grade is 62.78%. From this, it is known that the iron content of the obtained concentrate grade is only 54.49% when using the technology without circulating barrel equipment, and the obtained concentrate grade is only 54.49%. The ore grade contains 62.78% iron.
Embodiment 3
[0029] Taking iron fine powder with 50% iron-containing sulfuric acid slag in An County, Mianyang as an example, the selection process is the same as Example 1. The difference is that the sulfuric acid slag is not crushed and directly enters the ball mill for grinding, and the finally obtained iron fine powder contains iron 62- 63%, the recovery rate is more than 70%, 5-7% higher than other dressing plants, the iron content is more than double, and the recovery rate is more than 10% higher.
[0030] Equally, detect the iron fine powder that this embodiment enters the circulation tank from the magnetic separation unit and the strong magnetic separator to get the grade iron content of 58% of this iron fine powder, detect the iron fine powder that enters the concentrate overflow pipe to get this The concentrate grade contains 61% iron. From this, it is known that when the process without circulating barrel equipment is used, the iron content of the concentrate grade is only 57%. ...
PUM
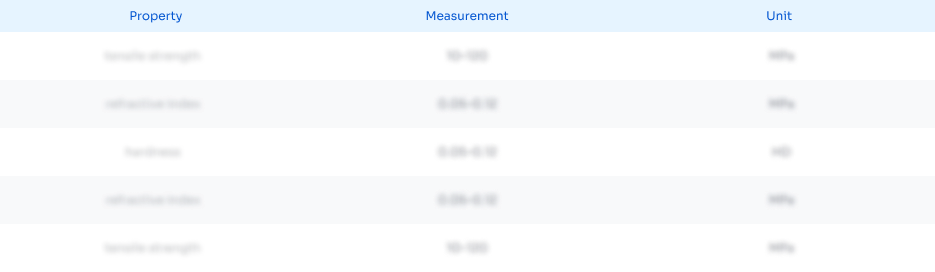
Abstract
Description
Claims
Application Information

- R&D Engineer
- R&D Manager
- IP Professional
- Industry Leading Data Capabilities
- Powerful AI technology
- Patent DNA Extraction
Browse by: Latest US Patents, China's latest patents, Technical Efficacy Thesaurus, Application Domain, Technology Topic, Popular Technical Reports.
© 2024 PatSnap. All rights reserved.Legal|Privacy policy|Modern Slavery Act Transparency Statement|Sitemap|About US| Contact US: help@patsnap.com