Method for removing nitrite ester in tail gas of production of oxalate through CO coupling
A technology for coupling oxalate and nitrite, applied in separation methods, chemical instruments and methods, and dispersed particle separation, etc., can solve the problems of high nitrogen oxide concentration and low nitrite removal rate.
- Summary
- Abstract
- Description
- Claims
- Application Information
AI Technical Summary
Problems solved by technology
Method used
Examples
Embodiment 1
[0012] Fully mix tail gas with 1% methyl nitrite content and reducing gas ammonia in a fixed-bed reactor, at a volume space velocity of 3000 hours -1 , the reaction temperature is 250°C, the reaction pressure is 0.2MPa, the molar ratio of reducing gas ammonia to methyl nitrite is 1, and the source of reducing gas ammonia is liquid ammonia. The catalyst is based on alumina as a carrier, the active component is selected from copper oxides, and the auxiliary agent is selected from manganese. Based on the carrier, the amount of copper oxides selected from the weight of copper is 20% by weight. Based on the weight of the additive manganese, the amount of oxides selected from manganese is 3% by weight, the conversion rate of methyl nitrite is 100%, and the content of nitrogen oxides in the tail gas is 5ppm.
[0013]
Embodiment 2
[0015] Fully mix tail gas with 2% ethyl nitrite content and reducing gas ammonia in a fixed-bed reactor, at a volume space velocity of 1000 hours -1 , the reaction temperature is 200°C, the reaction pressure is 0.3MPa, the molar ratio of reducing gas ammonia to ethyl nitrite is 1, the source of reducing gas ammonia is urea solution, and the concentration of urea solution is 50% The copper catalyst is contacted and fully reacted. The copper-containing catalyst uses alumina as a carrier, the active component is selected from copper oxides, and the auxiliary agent is selected from manganese and iron. Based on the carrier, based on the weight of elemental copper, selected from the oxidation of copper The amount of material used is 6% by weight, based on the weight of the additive elemental metal, the amount of oxides selected from manganese is 5% by weight, the amount of oxides selected from iron is 10% by weight, sub The conversion rate of ethyl nitrate is 100%, and the content o...
Embodiment 3
[0018] The tail gas with a methyl nitrite content of 0.3% and the reducing gas ammonia are fully mixed in a fixed bed reactor, and the volume space velocity is 300 hours -1 , the reaction temperature is 220°C, the reaction pressure is 0.5MPa, the molar ratio of reducing gas ammonia to methyl nitrite is 0.95, and the source of reducing gas ammonia is liquid ammonia. The catalyst is supported by alumina and silicon oxide (60% of which is alumina), the active component is selected from copper oxide, and the additive is selected from nickel. Based on the support, the weight of elemental copper is selected from the oxide of copper. The amount of substance used is 15% by weight, based on the weight of the nickel additive, the amount of oxides selected from nickel is 7% by weight, the conversion rate of methyl nitrite is 100%, and the nitrogen oxides in the exhaust gas The content is 30ppm.
[0019]
PUM
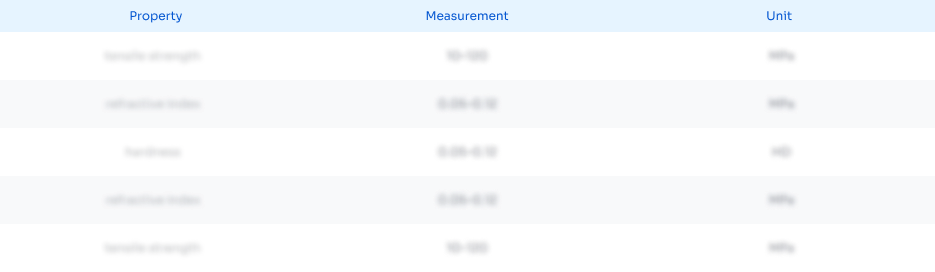
Abstract
Description
Claims
Application Information

- Generate Ideas
- Intellectual Property
- Life Sciences
- Materials
- Tech Scout
- Unparalleled Data Quality
- Higher Quality Content
- 60% Fewer Hallucinations
Browse by: Latest US Patents, China's latest patents, Technical Efficacy Thesaurus, Application Domain, Technology Topic, Popular Technical Reports.
© 2025 PatSnap. All rights reserved.Legal|Privacy policy|Modern Slavery Act Transparency Statement|Sitemap|About US| Contact US: help@patsnap.com