Method for processing optical active layer of polymer solar cell and polymer solar cell manufacturing method
A technology for solar cells and photoactive layers, applied in the field of polymer solar cells, can solve the problems of difficult to control the temperature and time of thermal annealing, small windows, etc., and achieve the effects of improving carrier mobility, low cost and high performance
- Summary
- Abstract
- Description
- Claims
- Application Information
AI Technical Summary
Problems solved by technology
Method used
Image
Examples
preparation example Construction
[0027] A method for processing a photoactive layer of a polymer solar cell and a method for preparing the cell thereof, the steps are as follows:
[0028] 1) Use glass or flexible plastic as the substrate 1, and use the transparent conductive film (TCO) as the front electrode 2, and clean them ultrasonically in deionized water, ethanol and acetone respectively;
[0029] 2) Prepare a layer of good hole (or electron) transport material as the first modification layer 3 on the surface of the dried front electrode by spin coating method, and the thickness of the first modification layer 3 is 1-100 nm;
[0030] 3) On the surface of the prepared first modification layer 3, polythiophene (P 3 HT) The blending system of donor material and acceptor material is used as the photoactive layer 4, and spin coating is performed by adjusting the room temperature, the speed and time of spin coating film formation, and let the film stand in the air to dry naturally after spin coating;
[0031]...
Embodiment 1
[0036]A transparent conductive film (ITO) glass substrate was used as the front electrode of the organic battery, which were cleaned ultrasonically in deionized water, ethanol and acetone, and dried. Spin coating (5000rpm, 60s) on the surface of the dried front electrode to prepare a layer of poly3,4-ethylenedioxythiophene monomer-doped polystyrene sulfonic acid (PEDOT:PSS) with good hole transport material As the first finishing layer, and dry with heat. Next, a photoactive layer is spin-coated on the substrate coated with the hole transport layer. Photoactive layer solution preparation: weigh a certain amount of electron donor (P 3 HT) and the acceptor material fullerene derivative (PC60BM) were dissolved in the organic solvent chlorobenzene with a solution concentration of 10 mg / ml, and stirred evenly by ultrasonic to form a mixed solvent. In the air, the active layer was processed by adjusting the temperature, the rotational speed of spin coating and the time. The experi...
Embodiment 2
[0042] A transparent conductive film (ITO) glass substrate was used as the front electrode of the organic battery, which were cleaned ultrasonically in deionized water, ethanol and acetone, and dried. Spin coating (5000rpm, 60s) on the surface of the dried front electrode to prepare a layer of poly3,4-ethylenedioxythiophene monomer-doped polystyrene sulfonic acid (PEDOT:PSS) with good hole transport material As the first finishing layer, and dry with heat. Next, a photoactive layer is spin-coated on the substrate coated with the hole transport layer. Photoactive layer solution preparation: weigh a certain amount of electron donor (P 3 HT) and the acceptor material fullerene derivative (PC60BM) were dissolved in the organic solvent chlorobenzene with a solution concentration of 10 mg / mL, and stirred evenly by ultrasonic to form a mixed solvent. In the air, the photoactive layer was processed by adjusting the temperature, the rotational speed of spin coating and the time. The ...
PUM
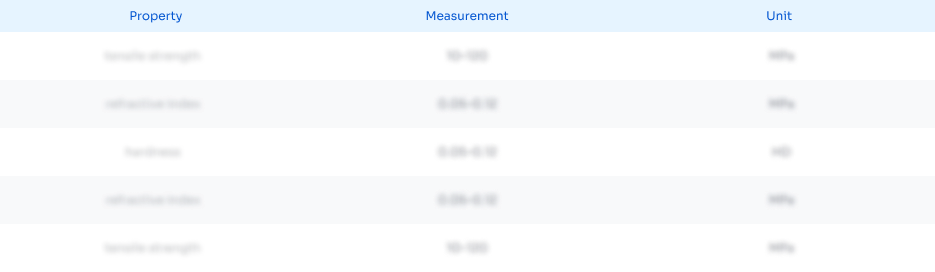
Abstract
Description
Claims
Application Information

- R&D
- Intellectual Property
- Life Sciences
- Materials
- Tech Scout
- Unparalleled Data Quality
- Higher Quality Content
- 60% Fewer Hallucinations
Browse by: Latest US Patents, China's latest patents, Technical Efficacy Thesaurus, Application Domain, Technology Topic, Popular Technical Reports.
© 2025 PatSnap. All rights reserved.Legal|Privacy policy|Modern Slavery Act Transparency Statement|Sitemap|About US| Contact US: help@patsnap.com