Manufacturing method of anti-biotic and anti-static yarn dyed fabric
An anti-static, fabric technology, applied in fabrics, textiles, rayon manufacturing and other directions, can solve the problems of energy and dye waste, high dye consumption, strict dyeing requirements, etc., to save wastewater treatment, avoid environmental pollution, and reduce dyeing. cost effect
- Summary
- Abstract
- Description
- Claims
- Application Information
AI Technical Summary
Problems solved by technology
Method used
Examples
Embodiment 1
[0022] A preparation method of antibacterial and antistatic yarn-dyed fabric, comprising the following steps:
[0023] (1) Selection of raw materials: choose chitin fiber, white cotton fiber and short chemical fiber as raw materials;
[0024] (2) Dyeing: Dye chitin fiber, white cotton fiber, and short chemical fiber with masterbatch. The specific steps are: add 4% of the weight of dark green masterbatch to chitin fiber, mix well and then add In the screw spinning machine, through the screw spinning machine, the melt after mixing and reacting the chitin fiber and the dark green color masterbatch is spun to obtain the colored chitin fiber; then the white cotton fiber is dyed: in the white cotton fiber Add 4% green color masterbatch of its weight, mix evenly and produce colored cotton fiber through high-temperature melt extrusion spinning; carry out the same dyeing treatment on chemical fiber staple fibers: add 5% green color masterbatch to chemical fiber staple fibers , mixed e...
Embodiment 2
[0032] A preparation method of antibacterial and antistatic yarn-dyed fabric, comprising the following steps:
[0033] (1) Selection of raw materials: choose chitin fiber, white cotton fiber and short chemical fiber as raw materials;
[0034] (2) Dyeing: Dye chitin fiber, white cotton fiber, and short chemical fiber with masterbatch. The specific steps are: add 5% of the weight of light red masterbatch to chitin fiber, mix well and then add In the screw spinning machine, through the screw spinning machine, the melt after mixing and reacting the chitin fiber and the light red color masterbatch is spun to obtain the colored chitin fiber; then the white cotton fiber is dyed: in the white cotton fiber Add 5% of its weight of purple color masterbatch, mix evenly and produce colored cotton fibers through high-temperature melt extrusion spinning; carry out the same dyeing treatment on chemical fiber staple fibers: add 6% light red masterbatch to chemical fiber staple fibers Granules...
PUM
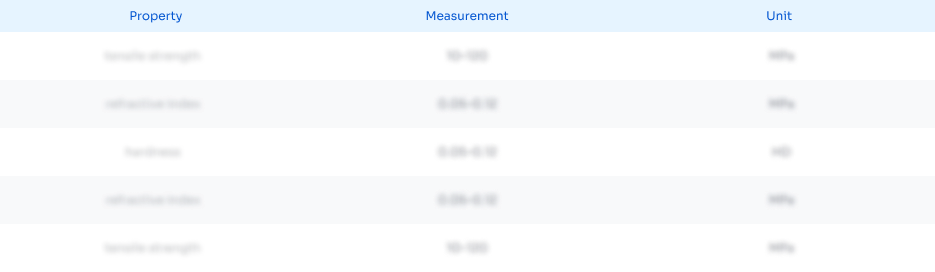
Abstract
Description
Claims
Application Information

- R&D
- Intellectual Property
- Life Sciences
- Materials
- Tech Scout
- Unparalleled Data Quality
- Higher Quality Content
- 60% Fewer Hallucinations
Browse by: Latest US Patents, China's latest patents, Technical Efficacy Thesaurus, Application Domain, Technology Topic, Popular Technical Reports.
© 2025 PatSnap. All rights reserved.Legal|Privacy policy|Modern Slavery Act Transparency Statement|Sitemap|About US| Contact US: help@patsnap.com