Preparation method of polycarboxylate water reducer macromonomer methallyl alcohol polyoxyethylene ether
A technology of methallyl alcohol polyoxyethylene ether and methallyl alcohol, which is applied in the field of preparation of polycarboxylate superplasticizer macromonomer methallyl alcohol polyoxyethylene ether, and can solve the difficulty of controlling the reaction process Large, prone to production accidents, complicated production process, etc., to achieve the effect of narrow relative molecular weight distribution, shortened production cycle, and simple production process
- Summary
- Abstract
- Description
- Claims
- Application Information
AI Technical Summary
Problems solved by technology
Method used
Image
Examples
Embodiment 1
[0032] Preparation of methallyl alcohol polyoxyethylene (55) ether:
[0033] Catalyst preparation: Add 1.39mol (100g) methallyl alcohol to a 100ml round-bottomed single-necked flask, put it on an electromagnetic stirrer with a water bath, and slowly add 0.0695mol (2.65g) lithium aluminum tetrahydride, the reaction temperature is 30°C, After 2 hours of reaction, the catalyst was prepared after the reaction was complete.
[0034] Add 1.39mol (100g) methallyl alcohol and the above-mentioned catalyst in a 10L pressure reactor, and connect the ethylene oxide metering tank to the pressure reactor. Replace the air in the kettle with nitrogen for 3 times, and when the temperature of the kettle rises to 80-85° C., 22.24 mol (979 g) of ethylene oxide is passed through for 4 hours, and the reaction is continued for 0.5 hours. Then add 2 g of potassium hydroxide, stir and heat up to 100-110° C., feed 130.6 mol (5749 g) of ethylene oxide for 8 hours, and continue the reaction for 0.5 hour...
Embodiment 2
[0036] Preparation of methallyl alcohol polyoxyethylene (57) ether:
[0037] Catalyst preparation: Add 1.39mol (100g) methallyl alcohol to a 100ml round-bottomed single-necked flask, put it on an electromagnetic stirrer with a water bath and slowly add 0.139mol (5.28g) lithium aluminum tetrahydride, the reaction temperature is 20°C, After 3 hours of reaction, the catalyst was prepared after the reaction was complete.
[0038] Add 1.39mol (100g) methallyl alcohol and the above-mentioned catalyst in a 10L pressure reactor, and connect the ethylene oxide metering tank to the pressure reactor. Replace the air in the kettle with nitrogen for 3 times, and when the temperature of the kettle rises to 80-85° C., 55.6 mol (2447 g) of ethylene oxide is passed through for 4 hours, and the reaction is continued for 0.5 hours. Then add 2g of sodium hydroxide, stir and raise the temperature to 110-120°C, and feed 102.9mol (4526g) of ethylene oxide for 8 hours to continue the reaction for 0....
Embodiment 3
[0040] Preparation of methallyl alcohol polyoxyethylene (60) ether:
[0041] Catalyst preparation: Add 1.39mol (100g) methallyl alcohol to a 100ml round-bottomed single-necked flask, put it on an electromagnetic stirrer with a water bath, and slowly add 0.104mol (3.97g) lithium aluminum tetrahydride, the reaction temperature is 10°C, After 5 hours of reaction, the catalyst was prepared after the reaction was complete.
[0042] Add 1.39mol (100g) methallyl alcohol and the above-mentioned catalyst in a 10L pressure reactor, and connect the ethylene oxide metering tank to the pressure reactor. Replace the air in the kettle with nitrogen for 3 times, and when the temperature of the kettle rises to 80-85° C., 38.92 mol (1713 g) of ethylene oxide is passed through for 4 hours, and the reaction is continued for 0.5 hours. Then add 1 g of sodium hydroxide and 1 g of potassium hydroxide, stir and heat up to 105-115° C., feed 127.9 mol (5627 g) of ethylene oxide for 8 hours, and contin...
PUM
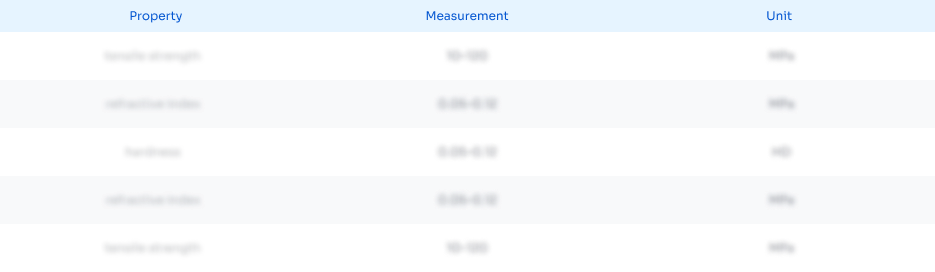
Abstract
Description
Claims
Application Information

- R&D
- Intellectual Property
- Life Sciences
- Materials
- Tech Scout
- Unparalleled Data Quality
- Higher Quality Content
- 60% Fewer Hallucinations
Browse by: Latest US Patents, China's latest patents, Technical Efficacy Thesaurus, Application Domain, Technology Topic, Popular Technical Reports.
© 2025 PatSnap. All rights reserved.Legal|Privacy policy|Modern Slavery Act Transparency Statement|Sitemap|About US| Contact US: help@patsnap.com