Method for preparing high-purity diethyl disulfide
A high-purity technology of diethyl disulfide, which is applied in the field of petrochemical industry, can solve the problems of inability to prepare high-purity diethyl disulfide in large quantities, reduce the discharge of three wastes and environmental pollution, reduce production costs, simplify The effect of the production process
- Summary
- Abstract
- Description
- Claims
- Application Information
AI Technical Summary
Problems solved by technology
Method used
Image
Examples
Embodiment 1
[0020] Such as figure 1 As shown, a method for preparing high-purity diethyl disulfide described in the embodiment of the present invention, its production process is: the petrochemical raw material rich in ethanethiol is subjected to the step of sweetening mercaptan with lye, and the step of catalytic oxidation of sulfur-containing and rich alkali , disulfide pre-distillation impurity removal step and disulfide rectification step to obtain high-purity diethyl disulfide;
[0021] The lye demercaptan step is as follows: mix ethanethiol-rich petrochemical raw materials with NaOH solution according to the volume ratio (1:1~5:1) and react at 25~45°C for 1~30 minutes to prepare mercaptan Sodium lye, its chemical reaction formula is: CH 3 -CH 2 -SH+NaOH→CH 3 -CH 2 -S-Na+H 2 O;
[0022] The described sulfur-containing alkali-rich catalytic oxidation step is: adding a phthalocyanine cobalt catalyst and an oxidant to the above-mentioned thiol-containing sodium lye for catalytic o...
Embodiment 2
[0027] Take 1L of crude oil with high ethanethiol content (100-20000??g / g) (represented by South Pass crude oil, but not limited thereto) or coking liquefied gas and mixed liquefied gas with high ethanethiol content during processing One of intermediate products such as gas, light naphtha, oil gas, condensate, etc., prepare 0.2L of NaOH solution with a concentration of 15-30%wt, and 10%wt of dinuclear phthalocyanine cobalt ammonium sulfonate catalyst solution as the experimental material 0.1 L; The oil product containing ethanethiol and NaOH solution are carried out sweetening reaction in the fiber liquid membrane or other similar high-efficiency mass transfer reactors according to the ratio of 5:1. After standing for 30 minutes, ethanethiol is converted into sodium mercaptide and separated into the lye phase; after the lye and oil are completely separated, add 20-2000?g of lye rich in sodium mercaptide to the catalyst / g, into the lye containing the catalyst, air or oxygen th...
Embodiment 3
[0029]After crude oil containing different sulfur forms is refined and processed, the total sulfur in the coking liquefied gas is 3800??g / g, of which ethanethiol accounts for 53% of the total sulfur. First, the coking liquefied gas is eluted with alkali to remove the mercaptan Then, the sulfide in the rich lye after sweetening is catalyzed and oxidized, and most of ethanethiol and a small amount of other mercaptans are finally converted into a disulfide mixture mainly composed of diethyl disulfide. Preliminary distillation is carried out on the disulfide separated by enrichment, and after most of the impurities such as sodium ions and cobalt ions are separated, the crude disulfide obtained is subjected to rectification or high gravity separation and purification. The difference is that the number of theoretical plates used in disulfide rectification is 40, the reflux ratio is 15, and the diethyl disulfide with a purity of 98.2% is obtained.
PUM
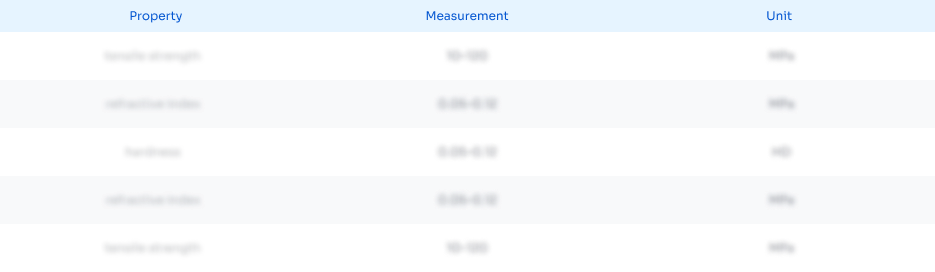
Abstract
Description
Claims
Application Information

- R&D
- Intellectual Property
- Life Sciences
- Materials
- Tech Scout
- Unparalleled Data Quality
- Higher Quality Content
- 60% Fewer Hallucinations
Browse by: Latest US Patents, China's latest patents, Technical Efficacy Thesaurus, Application Domain, Technology Topic, Popular Technical Reports.
© 2025 PatSnap. All rights reserved.Legal|Privacy policy|Modern Slavery Act Transparency Statement|Sitemap|About US| Contact US: help@patsnap.com