Defoamer for paper pulp and preparation method thereof
A technology of defoaming agent and pulp, applied in the direction of defoaming agent, etc., can solve problems such as defoaming difficulties, achieve good defoaming effect, promote uniform dispersion, promote compatibility and dispersibility
- Summary
- Abstract
- Description
- Claims
- Application Information
AI Technical Summary
Problems solved by technology
Method used
Image
Examples
Embodiment 1
[0024] (1) 30kg of polyethyl ether with a relative molecular weight of 2000, 20kg of sodium alginate, 12kg of polyethylene oxide with a relative molecular weight of 2000, 7kg of stearyl alcohol, 6kg of triolein and 1kg of sodium hydroxide at 55°C, add Mix in the high-pressure homogenizer for 1 hour, the homogenizing pressure of the first section of the high-pressure homogenizer is 17MPa, and the homogenizing pressure of the second section is 3MPa,
[0025] (2) cooling the product of step (1) to room temperature, adjusting its pH to 6.5 with hydrochloric acid to obtain a defoamer for pulp,
[0026] The performance test results of the prepared defoamer are shown in Table 1.
Embodiment 2
[0028] (1) Put 20k of polyethyl ether with a relative molecular weight of 4000, 30kg of sodium alginate, 10kg of polyethylene oxide with a relative molecular weight of 1500, 5kg of stearyl alcohol, 4kg of triolein and 2kg of sodium hydroxide at 45°C, Add in the high-pressure homogenizer and mix for 2 hours. The homogeneous pressure of the first section of the high-pressure homogenizer is 20MPa, and the homogeneous pressure of the second section is 4.9Mpa.
[0029] (2) Cool the product of step (1) to room temperature, adjust its pH to 6.5 with hydrochloric acid, and obtain a defoamer for pulp.
[0030] The performance test results of the prepared defoamer are shown in Table 1.
Embodiment 3
[0032] (1) Put 50k of polyethyl ether with a relative molecular weight of 3000, 20kg of sodium alginate, 14kg of polyethylene oxide with a relative molecular weight of 3000, 10kg of stearyl alcohol, 8kg of triolein and 0.5kg of sodium hydroxide at 50°C , added to the high-pressure homogenizer and mixed for 2 hours, the homogenizing pressure of the first section of the high-pressure homogenizer is 18MPa, and the homogenizing pressure of the second section is 4MPa,
[0033] (2) Cool the product of step (1) to room temperature, adjust its pH to 6.5 with hydrochloric acid, and obtain a defoamer for pulp.
[0034] The performance test results of the prepared defoamer are shown in Table 1.
[0035] Table 1
[0036]
[0037] The defoamer that the present invention makes has good defoaming effect, as can be seen from Table 1, the defoaming effect under 35 ℃ is better than the defoaming effect under 25 ℃, and this is because the component of defoamer is in When the temperatur...
PUM
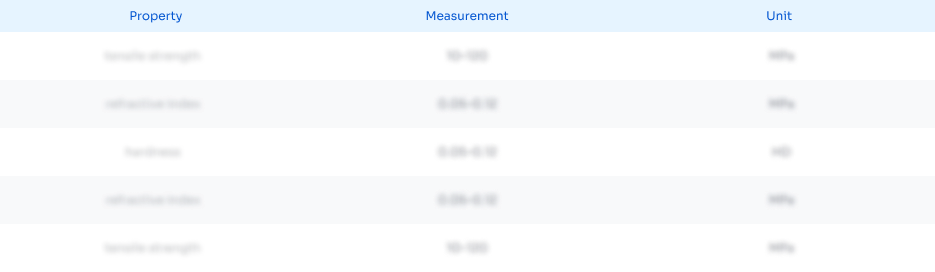
Abstract
Description
Claims
Application Information

- R&D Engineer
- R&D Manager
- IP Professional
- Industry Leading Data Capabilities
- Powerful AI technology
- Patent DNA Extraction
Browse by: Latest US Patents, China's latest patents, Technical Efficacy Thesaurus, Application Domain, Technology Topic, Popular Technical Reports.
© 2024 PatSnap. All rights reserved.Legal|Privacy policy|Modern Slavery Act Transparency Statement|Sitemap|About US| Contact US: help@patsnap.com