Method for determining amount of slagging material and deoxidized alloy added into LF (Low-Frequency) refining furnace by use of reference heat method
A technology for deoxidizing alloys and refining furnaces, applied in the direction of improving process efficiency, can solve problems such as ineffective methods for content control, and achieve the effects of optimizing refining effects, promoting standardized operations, and stabilizing the quality of refined molten steel
- Summary
- Abstract
- Description
- Claims
- Application Information
AI Technical Summary
Problems solved by technology
Method used
Image
Examples
Embodiment 1
[0065] After the furnace number 2-4479 ladle was transported into the LF refining furnace, the collected data: the steel grade number was SPHC, the dissolved oxygen in the molten steel at the end of the converter smelting was 883ppm, the weight of the molten steel was 130.9 tons, and the amount of Al-Mn ferro-manganese added during the tapping process of the converter was 400kg , Almanganese ferroalloy contains 55% aluminum, after calculating F=400*55%-130.9*883*1.125*0.001: the remaining aluminum content is 90.0kg after removing the dissolved oxygen in the molten steel during the tapping process.
[0066] Measure the dissolved oxygen content 8 (ppm) and the mass percentage of acid-soluble aluminum 0.005 (%) in LF incoming molten steel by using the oxygen-fixed probe. After calling the database, find the furnace number 3-3683 and furnace number 3-8311 2 heats of molten steel are used as reference heats, the dissolved oxygen (ppm) in the molten steel at the end of the converter ...
Embodiment 2
[0071] After the furnace number 3-8218 ladle was transported into the LF refining furnace, the collected data: the steel grade number is SPHC, the dissolved oxygen in the molten steel at the end of the converter smelting is 528ppm, the molten steel weighs 133.6 tons, and the amount of Al-Mn ferro-manganese added during the tapping process of the converter is 450kg , Almanganese ferromanganese contains 55% aluminum, calculated (450*55%-133.6*528*1.125*0.001): the remaining aluminum content after removing dissolved oxygen in molten steel during tapping process is 168.1kg; Measure the dissolved oxygen content of 10ppm and the mass percentage of acid-soluble aluminum of 0.005 (%) in LF's incoming molten steel. After calling the database, find 2 heats of steel with furnace number 3-8328 and furnace number 3-8327 as reference furnaces , dissolved oxygen (ppm) in molten steel at the end of converter smelting of these two furnaces of steel, the remaining aluminum content (kg) after rem...
PUM
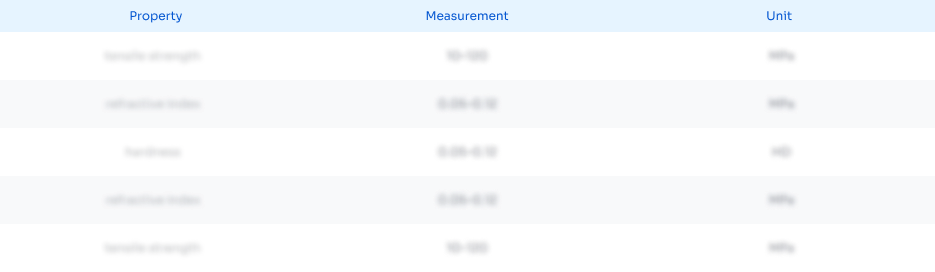
Abstract
Description
Claims
Application Information

- Generate Ideas
- Intellectual Property
- Life Sciences
- Materials
- Tech Scout
- Unparalleled Data Quality
- Higher Quality Content
- 60% Fewer Hallucinations
Browse by: Latest US Patents, China's latest patents, Technical Efficacy Thesaurus, Application Domain, Technology Topic, Popular Technical Reports.
© 2025 PatSnap. All rights reserved.Legal|Privacy policy|Modern Slavery Act Transparency Statement|Sitemap|About US| Contact US: help@patsnap.com