Method for producing carbonized material by means of carbonizing converter
A carbonized material and converter technology, which is applied in chemical instruments and methods, biofuels, coke ovens, etc., can solve the problems of increasing fuel costs, increasing exhaust gas emissions, and inconvenient production, and achieves the effect of reducing energy consumption and reducing emissions
- Summary
- Abstract
- Description
- Claims
- Application Information
AI Technical Summary
Problems solved by technology
Method used
Image
Examples
Embodiment Construction
[0012] Such as figure 1 As shown, a method for producing carbonized materials using a carbonization converter, the steps are as follows: feed raw materials from the feed end of the carbonization converter, and heat the raw materials step by step in the product channel of the carbonization converter, slowly heating from normal temperature to 400 ° C ~ 600 ° C , the raw material is dried, pyrolyzed and solidified in the product channel of the carbonization furnace to produce carbonized material, which is discharged from the discharge end of the carbonization converter; the dry distillation gas volatilized during the drying, pyrolysis and solidification process of the raw material is controlled by negative pressure It moves in the same direction as the raw material, and is drawn into the incinerator through the pipe connected to the incinerator at the discharge end of the carbonization converter for incineration; part of the high-temperature gas generated after the incineration of...
PUM
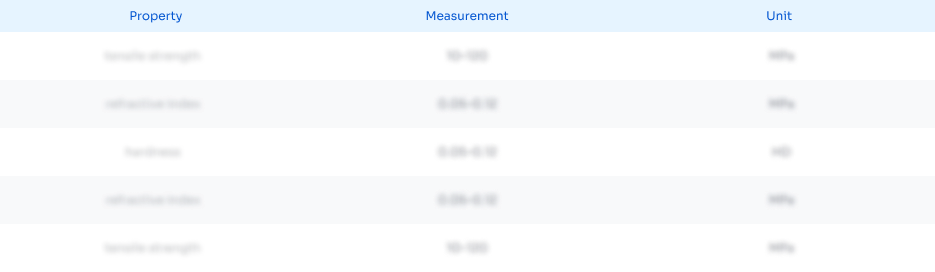
Abstract
Description
Claims
Application Information

- Generate Ideas
- Intellectual Property
- Life Sciences
- Materials
- Tech Scout
- Unparalleled Data Quality
- Higher Quality Content
- 60% Fewer Hallucinations
Browse by: Latest US Patents, China's latest patents, Technical Efficacy Thesaurus, Application Domain, Technology Topic, Popular Technical Reports.
© 2025 PatSnap. All rights reserved.Legal|Privacy policy|Modern Slavery Act Transparency Statement|Sitemap|About US| Contact US: help@patsnap.com