Hydrophilic polyvinylidene fluoride-based hollow-fiber separation membrane, and method for manufacturing same
A polyvinylidene fluoride and fiber separation technology, which is applied in semipermeable membrane separation, chemical instruments and methods, membranes, etc., can solve problems such as weak breaking strength and coating layer peeling, and achieve small pore size, excellent mechanical strength, The effect of excellent membrane fouling resistance
- Summary
- Abstract
- Description
- Claims
- Application Information
AI Technical Summary
Problems solved by technology
Method used
Image
Examples
Embodiment 1
[0054] Polyvinylidene fluoride resin (PVDF, Solvay (Solvay), solef6010) 35% by weight, γ-butyrolactone (GBL) 55% by weight, polyetherimide (PEI, SABIC innovation plasitics) company, ULTEM1010) were mixed at 10% by weight, stirred in a reactor at 170°C filled with nitrogen for 12 hours, and then transferred to a stabilization tank under the same state for 12 hours to prepare a spinning composition. Then, the spinning composition and the internal coagulation bath (GBL80% by weight, water 20% by weight) are simultaneously sprayed through the nozzle to form a hollow fiber, and immersed in the non-solvent contained in the external coagulation bath (phase transfer tank), Thus, a hollow fiber membrane is formed. Pure water was used as the non-solvent, the constant pump speed of the internal coagulation bath was 4.5ml / min, and the temperature was 25°C. In order to transfer the spinning solution, the nitrogen pressure in the reactor was set to 5kgf / cm as the discharge pressure 2 As a...
Embodiment 2
[0057] A hollow fiber separation membrane was produced in the same manner as in Example 1, except that polyimide (PI, Ciba polymer company, Matrimid 5218) was used instead of polyetherimide in Example 1.
Embodiment 3
[0059] A hollow fiber separation membrane was produced in the same manner as in Example 1, except that polyamide (PA, EMS-Grivory, Grivory G16) was used instead of polyetherimide in Example 1.
PUM
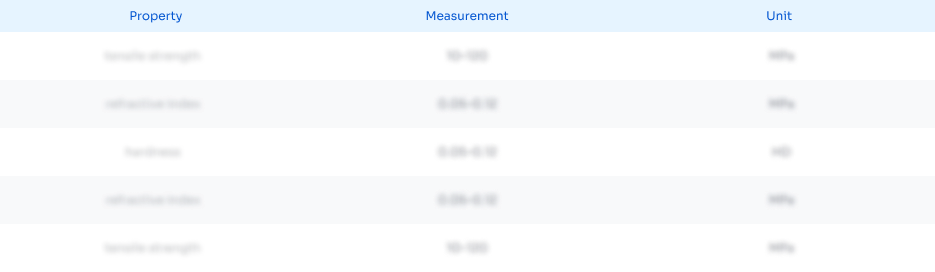
Abstract
Description
Claims
Application Information

- R&D Engineer
- R&D Manager
- IP Professional
- Industry Leading Data Capabilities
- Powerful AI technology
- Patent DNA Extraction
Browse by: Latest US Patents, China's latest patents, Technical Efficacy Thesaurus, Application Domain, Technology Topic, Popular Technical Reports.
© 2024 PatSnap. All rights reserved.Legal|Privacy policy|Modern Slavery Act Transparency Statement|Sitemap|About US| Contact US: help@patsnap.com