A connection structure between the thermal electrode of the vacuum hot pressing sintering furnace and the piston head of the hydraulic cylinder
A technology of vacuum hot pressing sintering and connection structure, which is applied in furnaces, muffle furnaces, cooking furnaces, etc. It can solve the problems of aging and brittleness of insulating sleeves, affecting unevenness and parallelism, and inconvenient disassembly and assembly, so as to increase the effective The effect of contact area, product quality assurance, and easy maintenance and disassembly
- Summary
- Abstract
- Description
- Claims
- Application Information
AI Technical Summary
Problems solved by technology
Method used
Image
Examples
Embodiment 1
[0022] see image 3 and Figure 4 , In this example, the connection structure between the hot electrode and the hydraulic cylinder piston head is composed of the hydraulic cylinder piston head 5 , the pressure plate 1 , the insulating plate 2 and the hot electrode 3 connected in sequence. Among them, the pressure plate 1 is welded on the end face of the piston head 5, and the pressure plate 1 and the insulating plate 2 are fixed together by four screws 4 evenly distributed; the insulating plate 2 and the hot electrode 3 are connected by a dovetail groove, and the dovetail groove connection structure The dovetail is arranged on the insulating plate 2, and the dovetail groove is arranged on the hot electrode 3, and the matching mode of the two is static fit. The material of the insulating plate 2 in the above connection structure is an epoxy resin plate.
Embodiment 2
[0024] see Figure 5 and Image 6 The difference between this embodiment and Embodiment 1 is: 1. The dovetail groove in the dovetail groove connection structure is arranged on the insulating plate 2, and the dovetail is arranged on the hot electrode 3. 2. The material of the insulating plate 2 is a polytetrafluoroethylene plate. The other structures of the connection structure of this example are the same as those of the first embodiment.
PUM
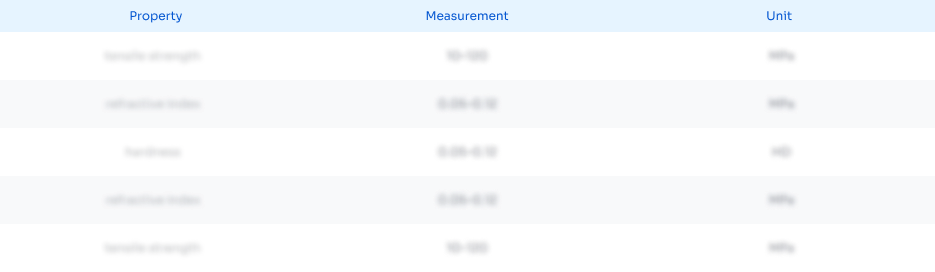
Abstract
Description
Claims
Application Information

- Generate Ideas
- Intellectual Property
- Life Sciences
- Materials
- Tech Scout
- Unparalleled Data Quality
- Higher Quality Content
- 60% Fewer Hallucinations
Browse by: Latest US Patents, China's latest patents, Technical Efficacy Thesaurus, Application Domain, Technology Topic, Popular Technical Reports.
© 2025 PatSnap. All rights reserved.Legal|Privacy policy|Modern Slavery Act Transparency Statement|Sitemap|About US| Contact US: help@patsnap.com