Liquefied gas desulfurization refining device and liquefied gas desulfurization refining method in oil refinery
A technology for liquefied gas and oil refinery, which is applied in the field of liquefied gas desulfurization and refining equipment in oil refineries, can solve problems such as blockage of trays or packing, large fluctuation of hydrogen sulfide, and decreased effect of hydrogen sulfide, etc. Effect
- Summary
- Abstract
- Description
- Claims
- Application Information
AI Technical Summary
Problems solved by technology
Method used
Image
Examples
Embodiment Construction
[0017] The present invention will be further described below in conjunction with the accompanying drawings and embodiments.
[0018] Such as figure 1 as shown, figure 1 It is a schematic diagram of the liquefied gas desulfurization and refining device of the present invention. The liquefied gas desulfurization and refining device of the present invention includes a buffer tank 1, an extraction tower 2, an MDEA solvent storage tank 12, an alkali storage tank 10, a water storage tank 11, and a primary extraction tank. Extraction settling tank 5, secondary extraction settling tank 7 and tertiary extraction settling tank 9, the outlet of buffer tank 1 is connected to the bottom inlet of extraction tower 2, and the top outlet of extraction tower 2 passes through coalescer 3 and primary fiber membrane The contactor 4 is connected to the primary extraction and settling tank 5, and the MDEA solvent storage tank 12 is respectively connected with the upper inlet of the extraction tower...
PUM
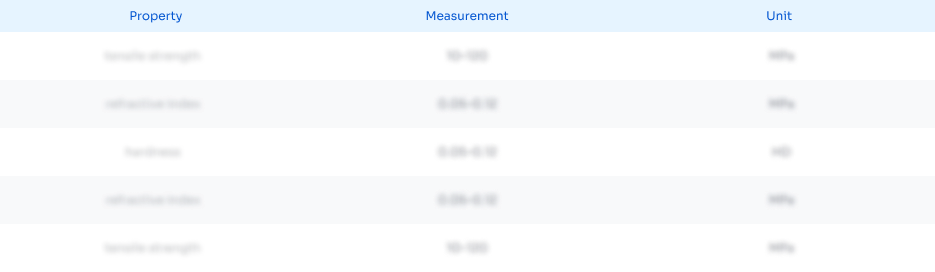
Abstract
Description
Claims
Application Information

- R&D Engineer
- R&D Manager
- IP Professional
- Industry Leading Data Capabilities
- Powerful AI technology
- Patent DNA Extraction
Browse by: Latest US Patents, China's latest patents, Technical Efficacy Thesaurus, Application Domain, Technology Topic, Popular Technical Reports.
© 2024 PatSnap. All rights reserved.Legal|Privacy policy|Modern Slavery Act Transparency Statement|Sitemap|About US| Contact US: help@patsnap.com