Fixture structure for machining herringbone groove in plunger part
A technology of herringbone grooves and plugs, which is applied in the direction of manufacturing tools, metal processing equipment, metal processing machinery parts, etc., to achieve the effect of ensuring stability, high processing efficiency and simple structure
- Summary
- Abstract
- Description
- Claims
- Application Information
AI Technical Summary
Problems solved by technology
Method used
Image
Examples
Embodiment Construction
[0010] The specific implementation manner of the present invention will be described below in conjunction with the accompanying drawings.
[0011] Such as figure 1 As shown, a fixture structure for processing herringbone grooves of plunger parts includes a fixture body 1 and a flat seat 2 that are fixed to each other. In the top seat 10, the spring 8 is set on the outer periphery of the set screw 9, and at the end of the set screw 9, the female top 7 is also installed in the top seat 10; Locking and positioning by the locking screw 401 , the knurled screw 3 is symmetrically installed on both sides of the flat seat 2 , and its end extends into the flat seat 2 and abuts against the flat post 4 .
[0012] Concrete work process of the present invention is as follows:
[0013] First, clamp body 1 of the present invention is installed on the chuck of the machine tool, then one end of plunger part 5 is abutted against female tip 7, female tip 7 is stressed and elastically lifted by...
PUM
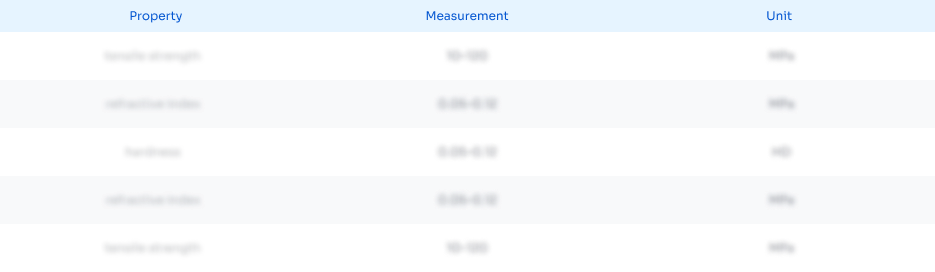
Abstract
Description
Claims
Application Information

- R&D
- Intellectual Property
- Life Sciences
- Materials
- Tech Scout
- Unparalleled Data Quality
- Higher Quality Content
- 60% Fewer Hallucinations
Browse by: Latest US Patents, China's latest patents, Technical Efficacy Thesaurus, Application Domain, Technology Topic, Popular Technical Reports.
© 2025 PatSnap. All rights reserved.Legal|Privacy policy|Modern Slavery Act Transparency Statement|Sitemap|About US| Contact US: help@patsnap.com