Flame-retardant finishing method for polyester fabric
A polyester fabric, flame retardant finishing technology, applied in fiber processing, textile and paper making, fiber type, etc., to achieve good flame retardant durability
- Summary
- Abstract
- Description
- Claims
- Application Information
AI Technical Summary
Problems solved by technology
Method used
Examples
Embodiment 1
[0012] A method for flame-retardant finishing of polyester fabrics, comprising the steps of:
[0013] 1) Mix 2 parts of hydroxypropyl methylcellulose, 9 parts of aluminum zirconate coupling agent, and 15 parts of tetrakishydroxymethyl phosphine chloride, and then slowly add 20 parts of cyclic phosphonate and 35 parts of zirconia at the same time, The feeding is completed within 20 minutes, and the mixing is continued for 25 minutes to obtain a composite flame retardant;
[0014] 2) Soak the polyester fabric in the dipping solution containing 60% composite flame retardant at 65°C for 2 hours;
[0015] 3) Keep the polyester fabric at 150°C for 4 hours after taking it out.
Embodiment 2
[0017] A method for flame-retardant finishing of polyester fabrics, comprising the steps of:
[0018] 1) Mix 1 part of hydroxypropyl methylcellulose, 8 parts of aluminum zirconate coupling agent, and 10 parts of tetrakishydroxymethylphosphine chloride, and then slowly add 15 parts of cyclic phosphonate and 30 parts of zirconia at the same time, The feeding is completed within 15 minutes, and the mixing is continued for 20 minutes to obtain a composite flame retardant;
[0019] 2) Soak the polyester fabric in the dipping solution containing 55% composite flame retardant at 60°C for 1 hour;
[0020] 3) Keep the polyester fabric at 145°C for 3 hours after taking it out.
Embodiment 3
[0022] A method for flame-retardant finishing of polyester fabrics, comprising the steps of:
[0023] 1) Mix 1.2 parts of hydroxypropyl methylcellulose, 8.9 parts of aluminum zirconate coupling agent, and 13 parts of tetrakishydroxymethyl phosphine chloride, and then slowly add 16 parts of cyclic phosphonate and 34 parts of zirconia at the same time, The feeding is completed within 17 minutes, and the mixing is continued for 23 minutes to obtain a composite flame retardant;
[0024] 2) Soak the polyester fabric in the dipping solution containing 57% composite flame retardant at 63°C for 1.5 hours;
[0025] 3) Keep the polyester fabric at 147°C for 3.5 hours after taking it out.
PUM
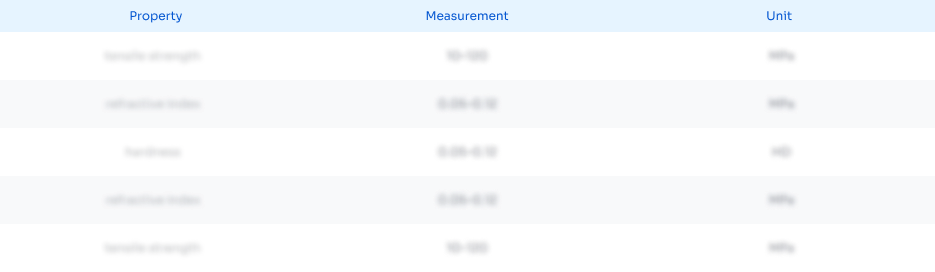
Abstract
Description
Claims
Application Information

- Generate Ideas
- Intellectual Property
- Life Sciences
- Materials
- Tech Scout
- Unparalleled Data Quality
- Higher Quality Content
- 60% Fewer Hallucinations
Browse by: Latest US Patents, China's latest patents, Technical Efficacy Thesaurus, Application Domain, Technology Topic, Popular Technical Reports.
© 2025 PatSnap. All rights reserved.Legal|Privacy policy|Modern Slavery Act Transparency Statement|Sitemap|About US| Contact US: help@patsnap.com