Foam concrete foaming agent and preparation method thereof
A foamed concrete and foaming agent technology, applied in the field of engineering materials, can solve the problems of poor foam stability and foaming ratio, low foaming power, poor foam stability, etc.
- Summary
- Abstract
- Description
- Claims
- Application Information
AI Technical Summary
Problems solved by technology
Method used
Image
Examples
preparation example Construction
[0022] Such as figure 1 Shown, the preparation method of a kind of foam concrete blowing agent of the present invention, comprises the steps:
[0023] Step 10. Prepare the ingredients according to the following volume ratio: 100% water; 6-10% saponin; 2-5% sodium dodecyl sulfonate; 1-4% polyethylene glycol; 0.02% benzoic acid ~3%; cellulose 0.8~3%;
[0024] Step 20, place water, saponin, sodium dodecyl sulfonate, polyethylene glycol, and cellulose in a hydrothermal synthesis reactor to react for 3 to 5 hours; the temperature of the hydrothermal synthesis reactor is limited to 60 ~80°C;
[0025] Step 30, after cooling the solution prepared by the reaction to room temperature, add benzoic acid, stir evenly, and then discharge.
Embodiment 1
[0027] Example 1: 100kg of water, 7kg of saponin, 3kg of sodium dodecyl sulfonate, 3kg of polyethylene glycol and 1.2kg of cellulose are placed in a hydrothermal synthesis reactor at (60-80) After reacting at ℃ for 4-5 hours, cooling the prepared solution to room temperature, adding 1 kg of benzoic acid, and stirring evenly, the foamed concrete foaming agent was prepared. According to the standard JG / T266-2011 "Foamed Concrete", the foaming agent was tested, and the test results were as follows: the foaming ratio was 67, the settlement distance was 4mm, and the bleeding volume was 28ml. The performance of the above foaming agent was tested The result is better than the technical requirements of the blowing agent in the standard.
Embodiment 2
[0028] Embodiment two: the water of 100kg, the saponin of 9kg, the sodium dodecyl sulfonate of 3kg, the polyethylene glycol of 3.6kg, the cellulose of 1.5kg are placed in the hydrothermal synthesis reactor at (60- 80) React at ℃ for 4-5 hours, cool the prepared solution to room temperature, then add 0.8 kg of benzoic acid, stir evenly, and prepare the foam concrete foaming agent. According to the standard JG / T266-2011 "Foamed Concrete", the foaming agent was tested, and the test results were as follows: the foaming ratio was 82, the settlement distance was 6mm, and the bleeding amount was 32ml. The performance of the above foaming agent was tested The result is better than the technical requirements of the blowing agent in the standard.
PUM
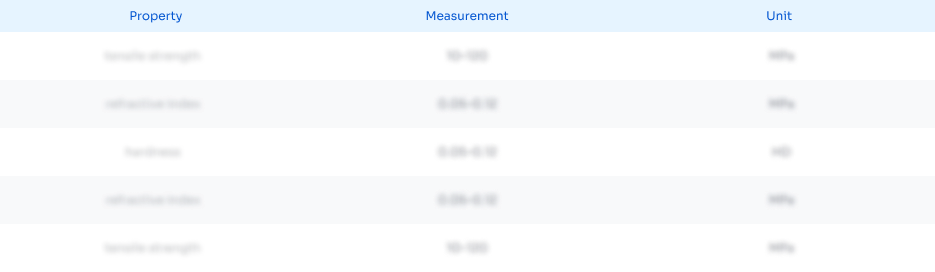
Abstract
Description
Claims
Application Information

- R&D
- Intellectual Property
- Life Sciences
- Materials
- Tech Scout
- Unparalleled Data Quality
- Higher Quality Content
- 60% Fewer Hallucinations
Browse by: Latest US Patents, China's latest patents, Technical Efficacy Thesaurus, Application Domain, Technology Topic, Popular Technical Reports.
© 2025 PatSnap. All rights reserved.Legal|Privacy policy|Modern Slavery Act Transparency Statement|Sitemap|About US| Contact US: help@patsnap.com