Converter gas mass-energy conversion and CO2 cycle steelmaking method
A converter gas and CO2 technology, applied in the manufacture of converters, furnaces, furnace components, etc., can solve the problem of low power consumption, achieve the effects of reducing CO2 emissions, realizing circular economy, and reducing oxidation and evaporation
- Summary
- Abstract
- Description
- Claims
- Application Information
AI Technical Summary
Problems solved by technology
Method used
Image
Examples
Embodiment Construction
[0021] 1. For the 120t converter slag splash protection process, the adsorption device is used to recover and separate the CO in the converter gas 2 and foreign CO 2 as CO 2 Air source for top blowing, bottom blowing and slag splashing. During top blowing, O 2 Mixed with 0.1% ~ 30% CO 2 When splashing slag, use the converter oxygen lance to switch and blow CO into the furnace 2 , the amount of carbon is 30~350kg, and the gas flow rate is 50000~60000Nm 3 / h, the working pressure of the gas is 0.7~0.9MPa. CO gas collected and enriched in converter gas can be used as an important energy source for metallurgy and can be used for waste heat air of hot blast stoves, coke ovens, power plant boilers, and steel rolling heating furnaces.
[0022] 2. For the 300t converter slag splash protection process, the adsorption device is used to recover and separate the CO in the converter gas 2 and foreign CO 2 as CO 2 Air source for top blowing, bottom blowing and slag splashing. Duri...
PUM
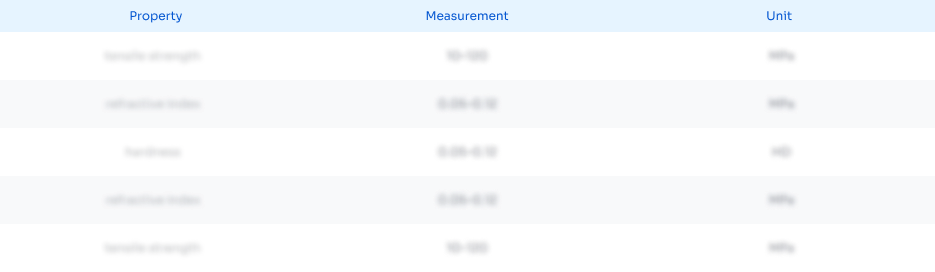
Abstract
Description
Claims
Application Information

- R&D
- Intellectual Property
- Life Sciences
- Materials
- Tech Scout
- Unparalleled Data Quality
- Higher Quality Content
- 60% Fewer Hallucinations
Browse by: Latest US Patents, China's latest patents, Technical Efficacy Thesaurus, Application Domain, Technology Topic, Popular Technical Reports.
© 2025 PatSnap. All rights reserved.Legal|Privacy policy|Modern Slavery Act Transparency Statement|Sitemap|About US| Contact US: help@patsnap.com