Method for removing silicon impurities in iron ore concentrate to improve grade of iron
A technology for removing iron and iron grade is applied in the field of removing silicon impurities in iron concentrate to improve iron grade, and can solve the problems of unsatisfactory removal of silicon impurities, unsatisfactory effect, and increased pollution, and achieves low cost and energy consumption. The effect of less and simple production process
- Summary
- Abstract
- Description
- Claims
- Application Information
AI Technical Summary
Problems solved by technology
Method used
Examples
Embodiment 1
[0015] (1) Crush and grind the magnetized roasted iron slag after pyrite acid production to 10mm;
[0016] (2) Add 100ml of the prepared silicate bacteria nitrogen-containing medium into a 250ml Erlenmeyer flask. The composition of the nitrogen-containing medium is: 3g of sucrose, Na 2 HPO 4 2g, MgSO 4 ·7H 2 O 0.5, (NH 4 ) 2 SO 4 1.5g, CaCO 3 0.1g, 1g bauxite, 1L single distilled water, pH value is 5, FeCl 3 FeCl with a mass volume ratio of 0.01g / ml to single distilled water 3 Solution 2ml, put the medium in a sterilizing pot at 121°C, and sterilize for 20 minutes;
[0017] (3) After the culture medium is cooled, transfer the culture bottle to a sterile bench, and after 25 minutes of ultraviolet sterilization, inoculate Bacillus circulans with an inoculation amount of 1%, place it on a constant temperature shaker at 30°C at 160rpm for 1 day, and then transfer it again , the inoculation amount was 1%, and the activated bacteria were transferred twice;
[0018] (4) ...
Embodiment 2
[0023] (1) Crush and grind the limonite to a particle size of 20mm.
[0024] (2) Add 100ml of the prepared silicate bacteria nitrogen-containing medium into a 250ml Erlenmeyer flask. The composition of the nitrogen-containing medium is: 4g of sucrose, Na 2 HPO 4 4g, MgSO 4 7H 2 O 0.7g, (NH 4 ) 2 SO 4 2.6g, CaCO 3 0.2g, 1g bauxite, 1L single distilled water, pH 6, FeCl 3 FeCl with a mass volume ratio of 0.01g / ml to single distilled water 3 Solution 2ml, put the culture medium in a sterilizing pot at 121°C, and sterilize for 20 minutes.
[0025] (3) After the culture medium is cooled down, transfer the culture bottle to a sterile bench, and after 25 minutes of ultraviolet sterilization, inoculate Acinetobacter with an inoculation volume of 1%, place it on a 30°C constant temperature shaker at 180rpm for 1 day, and then transfer it again. The inoculation volume was 1%, and the activated bacteria were transferred twice.
[0026] (4) Inoculate the Acinetobacter cultured ...
Embodiment 3
[0031] (1) Crush and grind the magnetized roasted iron slag after sulfuric acid production to 50mm.
[0032] (2) Add 100ml of the prepared silicate bacteria nitrogen-containing medium into a 250ml Erlenmeyer flask. The composition of the nitrogen-containing medium is: 5g of sucrose, Na 2 HPO 4 5g, MgSO 4 7H 2 O 1g, (NH 4 ) 2 SO 4 3.8g, CaCO 3 0.3g, 1g bauxite, 1L single distilled water, pH value is 7, FeCl 3 FeCl with a mass volume ratio of 0.01g / ml to single distilled water 3 Solution 2ml, put the culture medium in a sterilizing pot at 121°C, and sterilize for 20 minutes.
[0033] (3) After the culture medium is cooled, transfer the culture bottle to a sterile bench, and after 25 minutes of ultraviolet sterilization, inoculate Acinetobacter and Methylobacterium with an inoculation amount of 1%, and place it on a constant temperature shaker at 30°C at 200rpm for 1 day after activation. Transplanted once, the inoculation amount was 1%, and activated bacteria were tran...
PUM
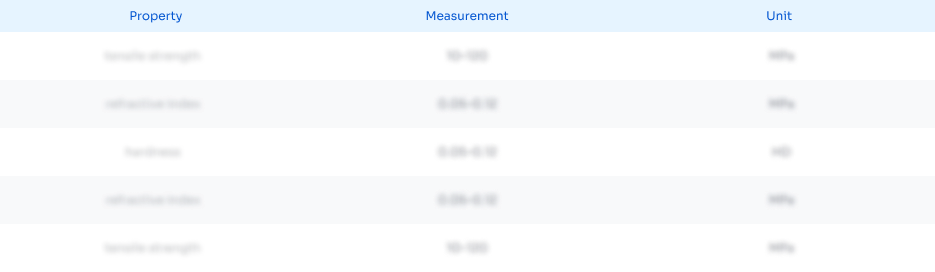
Abstract
Description
Claims
Application Information

- R&D
- Intellectual Property
- Life Sciences
- Materials
- Tech Scout
- Unparalleled Data Quality
- Higher Quality Content
- 60% Fewer Hallucinations
Browse by: Latest US Patents, China's latest patents, Technical Efficacy Thesaurus, Application Domain, Technology Topic, Popular Technical Reports.
© 2025 PatSnap. All rights reserved.Legal|Privacy policy|Modern Slavery Act Transparency Statement|Sitemap|About US| Contact US: help@patsnap.com