Regenerating method of waste sand of casting green sand
A green mold sand and abrasive technology, which is applied in the field of waste sand recycling, can solve the problems of difficult handling, damage to the strength of the original sand, and the inability to use foundry self-hardening sand and coated sand.
- Summary
- Abstract
- Description
- Claims
- Application Information
AI Technical Summary
Problems solved by technology
Method used
Examples
Embodiment 1
[0024] An embodiment of the method for recycling waste sand of casting green mold sand of the present invention, the method described in this embodiment includes the following steps:
[0025] (1) Add brown corundum abrasive to the green mold sand waste sand that has been crushed and screened, wherein the quality of brown corundum abrasive is 5% of the mass of green mold sand waste sand, and the particle size of brown corundum abrasive is 6 mesh;
[0026] (2) Put the green mold sand waste sand mixed in step (1) and the brown corundum abrasive into the roasting furnace for boiling and roasting. The bulk density of the brown corundum abrasive in the roasting furnace is 1.5g / cm 3 , the roasting temperature is 650-700°C, and the roasting time is 6-8 hours;
[0027] (3) cooling the green mold sand waste sand and brown corundum abrasive after roasting in step (2);
[0028] (4) Sieve the green mold sand waste sand and brown corundum abrasive after cooling in step (3), and separate th...
Embodiment 2
[0031] An embodiment of the method for recycling waste sand of casting green mold sand of the present invention, the method described in this embodiment includes the following steps:
[0032] (1) Add brown corundum abrasive to the green mold sand waste sand that has been crushed and screened, wherein the quality of brown corundum abrasive is 6% of the mass of green mold sand waste sand, and the particle size of brown corundum abrasive is 10 mesh;
[0033] (2) Put the green mold sand waste sand mixed in step (1) and the brown corundum abrasive into the roasting furnace for boiling and roasting. The bulk density of the brown corundum abrasive in the roasting furnace is 1.52g / cm 3 , the roasting temperature is 650-700°C, and the roasting time is 6-8 hours;
[0034] (3) cooling the green mold sand waste sand and brown corundum abrasive after roasting in step (2);
[0035] (4) Sieve the green mold sand waste sand and brown corundum abrasive after cooling in step (3), and separate ...
Embodiment 3
[0038] An embodiment of the method for recycling waste sand of casting green mold sand of the present invention, the method described in this embodiment includes the following steps:
[0039] (1) Add brown corundum abrasive to the green mold sand waste sand that has been crushed and screened, wherein the quality of brown corundum abrasive is 8% of the mass of green mold sand waste sand, and the particle size of brown corundum abrasive is 16 mesh;
[0040] (2) Put the green mold sand waste sand mixed in step (1) and the brown corundum abrasive into the roasting furnace for boiling and roasting. The bulk density of the brown corundum abrasive in the roasting furnace is 1.56g / cm 3 , the roasting temperature is 650-700°C, and the roasting time is 6-8 hours;
[0041] (3) cooling the green mold sand waste sand and brown corundum abrasive after roasting in step (2);
[0042] (4) Sieve the green mold sand waste sand and brown corundum abrasive after cooling in step (3), and separate ...
PUM
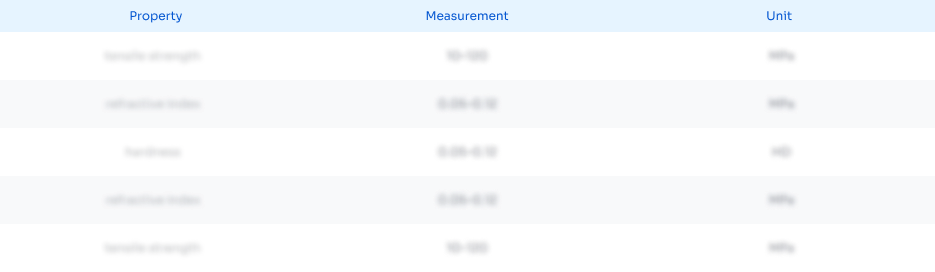
Abstract
Description
Claims
Application Information

- R&D
- Intellectual Property
- Life Sciences
- Materials
- Tech Scout
- Unparalleled Data Quality
- Higher Quality Content
- 60% Fewer Hallucinations
Browse by: Latest US Patents, China's latest patents, Technical Efficacy Thesaurus, Application Domain, Technology Topic, Popular Technical Reports.
© 2025 PatSnap. All rights reserved.Legal|Privacy policy|Modern Slavery Act Transparency Statement|Sitemap|About US| Contact US: help@patsnap.com