Polyurethane-water glass composite grouting material as well as preparation method and application thereof
A grouting material and water glass technology, applied in the field of building materials, can solve problems such as high cost, static electricity, secondary disasters, etc., and achieve the effects of compact consolidation, improved flame retardancy, and good compressive strength.
- Summary
- Abstract
- Description
- Claims
- Application Information
AI Technical Summary
Problems solved by technology
Method used
Image
Examples
Embodiment 1
[0032] (1) Preparation of polyurethane prepolymer
[0033] After dehydrating polyether polyol at 120°C and vacuum degree of 133.3Pa for 2 hours, add 32g of polyether N204, 50g of diphenylmethane diisocyanate (MDI) and 0.82g of benzoyl chloride into the container by one-time feeding method Mix and stir in a cold oil bath for 10 minutes, then raise the temperature and react at a constant temperature of 80°C for 3 hours, stop the reaction, and obtain a light-colored and transparent polyurethane prepolymer;
[0034] (2) Preparation of component A
[0035] Add 78g of polyurethane prepolymer to 10g of plasticizer, 10g of flame retardant tris(2-chloropropyl) phosphate (TCPP) and 2g of surfactant, mix and stir evenly to obtain component A;
[0036] (3) Preparation of component B
[0037] Stir 99.2g of sodium silicate and 0.8g of antistatic agent evenly to obtain component B;
[0038] (4) When in use, mix component A and component B according to the weight ratio of 1:1 and stir for ...
Embodiment 2
[0040] (1) Preparation of polyurethane prepolymer
[0041] After dehydrating polyether polyol at 120°C and vacuum degree of 133.3Pa for 2 hours, 16g of polyether N204, 6g of polyether N403, 60g of diphenylmethane diisocyanate (MDI) and 1.23g of benzene Add formyl chloride into the container and mix and stir in a cold oil bath for 20 minutes, then raise the temperature and react at a constant temperature of 75°C for 2.5 hours, stop the reaction, and obtain a light-colored and transparent polyurethane prepolymer.
[0042] (2) Preparation of component A
[0043] Add 77.5g of polyurethane prepolymer to 15g of plasticizer dibutyl phthalate (DBP), 5g of flame retardant tris(2-carboxyethyl)phosphine (TCEP) and 2.5g of surfactant hard foam silicone oil SD- 502, mix and stir evenly to obtain component A;
[0044] (3) Preparation of component B
[0045] Stir 99.5 g of potassium silicate and 0.5 g of antistatic agent evenly to obtain component B;
[0046] (4) When in use, mix compone...
Embodiment 3
[0048] (1) Preparation of polyurethane prepolymer
[0049] After dehydrating polyether polyol at 120°C and vacuum degree of 133.3Pa for 2 hours, 16g of polyether N204, 6g of polyether N403, 100g of diphenylmethane diisocyanate (MDI) and 1.22g of benzene Add formyl chloride into the container and mix and stir in a cold oil bath for 20 minutes, then raise the temperature and react at a constant temperature of 75°C for 2.5 hours, stop the reaction, and obtain a light-colored and transparent polyurethane prepolymer.
[0050] (2) Preparation of component A
[0051]Add 83g of polyurethane prepolymer to 5g of plasticizer dibutyl phthalate (DBP), 10g of flame retardant tris(2-chloropropyl) phosphate (TCPP) and 2g of surfactant hard foam silicone oil SD-502 , mixed and stirred evenly to obtain component A;
[0052] (3) Preparation of component B
[0053] Stir 99.2g of sodium silicate and 0.8g of antistatic agent evenly to obtain component B;
[0054] (4) When in use, mix component ...
PUM
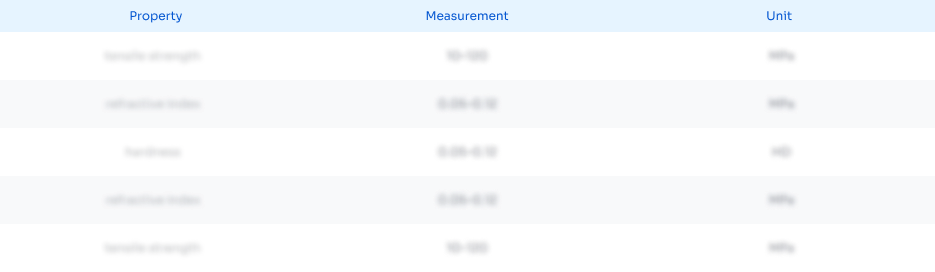
Abstract
Description
Claims
Application Information

- R&D
- Intellectual Property
- Life Sciences
- Materials
- Tech Scout
- Unparalleled Data Quality
- Higher Quality Content
- 60% Fewer Hallucinations
Browse by: Latest US Patents, China's latest patents, Technical Efficacy Thesaurus, Application Domain, Technology Topic, Popular Technical Reports.
© 2025 PatSnap. All rights reserved.Legal|Privacy policy|Modern Slavery Act Transparency Statement|Sitemap|About US| Contact US: help@patsnap.com