Clean production method of chlorinated polyethylene
A technology for chlorinated polyethylene and cleaner production, applied in the field of cleaner production of chlorinated polyethylene, can solve the problems of difficulty in recycling, large discharge of waste water, heavy environmental pollution, etc. Process efficient effect
- Summary
- Abstract
- Description
- Claims
- Application Information
AI Technical Summary
Problems solved by technology
Method used
Examples
Embodiment 1
[0019] at 12.5m 3 In the chlorination reactor, inject 9720Kg of hydrochloric acid solution with a concentration of 17wt%, add 1100Kg of high-density polyethylene, 0.6Kg of fatty alcohol polyoxyethylene ether and 12Kg of talcum powder, stir for 5 minutes, prepare a suspension solution, and seal the reactor.
[0020] Pass 900Kg liquid chlorine into the suspension solution in the reactor to carry out chlorination reaction, the reaction temperature is 50-130° C., and the reaction time is 3.5 hours to obtain chlorinated polyethylene slurry.
[0021] After cooling down, the chlorinated polyethylene slurry is transported to the filter washer, and through the synchronous cooperation of the rotating filter disc and the filter controller, the filter is divided into two sections to realize two-stage cleaning of the slurry. Stage filtration deacidification, the chlorinated polyethylene slurry passes through the first stage filter section, the concentrated hydrochloric acid contained in th...
Embodiment 2
[0024] at 60m 3 In the chlorination reactor, inject 43200 Kg of hydrochloric acid solution with a concentration of 22wt%, add 5500 Kg of high-density polyethylene, 1.5 Kg of polyvinylpyrrolidone and 55 Kg of amorphous silicon dioxide, stir for 10 minutes, prepare a suspension solution, and seal the reactor .
[0025] Pass 4800Kg liquid chlorine into the suspension solution in the reactor to carry out chlorination reaction, the reaction temperature is 30-130° C., and the reaction time is 5 hours to obtain chlorinated polyethylene slurry.
[0026] After cooling down, the chlorinated polyethylene slurry is transported to the filter washer, and through the synchronous cooperation of the rotating filter disc and the filter controller, the filter is divided into two sections to realize two-stage cleaning of the slurry. Stage filtration deacidification, the chlorinated polyethylene slurry passes through the first stage filter section, the concentrated hydrochloric acid contained in ...
PUM
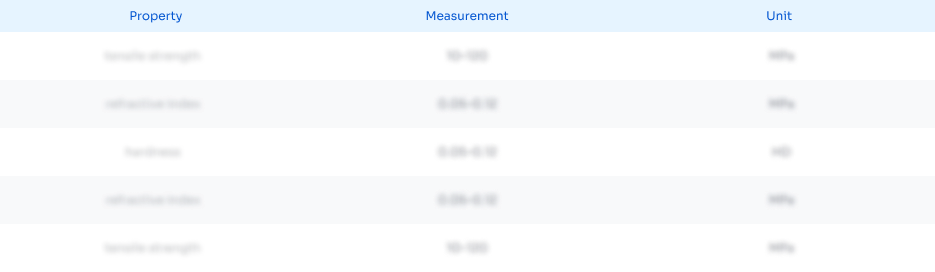
Abstract
Description
Claims
Application Information

- R&D
- Intellectual Property
- Life Sciences
- Materials
- Tech Scout
- Unparalleled Data Quality
- Higher Quality Content
- 60% Fewer Hallucinations
Browse by: Latest US Patents, China's latest patents, Technical Efficacy Thesaurus, Application Domain, Technology Topic, Popular Technical Reports.
© 2025 PatSnap. All rights reserved.Legal|Privacy policy|Modern Slavery Act Transparency Statement|Sitemap|About US| Contact US: help@patsnap.com