Method of coal blending for coking by steam coal pretreatment
A coal blending coking and thermal coal technology, applied in the field of metallurgical coke, can solve the problems of low volatile matter, reducing coke coldness, hot peptide strength, coke lumpiness, poor colloid fusion ability, etc.
- Summary
- Abstract
- Description
- Claims
- Application Information
AI Technical Summary
Problems solved by technology
Method used
Image
Examples
Embodiment
[0015] The process flow chart of the present invention: thermal coal→low temperature dry distillation→crushing→mixing with other coking coal in proportion→coking.
[0016] The operation steps of this method:
[0017] 1) Choose steam coal as lignite or long-flame coal or weakly caking coal or non-caking coal;
[0018] 2) Steam coal dry distillation: put steam coal in the furnace and dry distillation at 550°C until the volatile matter Vdaf is 20%, then grind it to 0.95mm with a grid-type ball mill (¢2700*3600), and set aside;
[0019] 3) Coal blending: mix dry distillation steam coal and coking coal at a weight percentage of 0.05-0.08:1, and charge into the furnace for coking;
[0020] Among them, mixed coal blending: carbonized steam coal is mixed with other coking coals at a ratio of 5%, and then loaded into the furnace for coking; the coking coals selected are: coking coal, fat coal, gas coal, gas fat coal, and 1 / 3 coking coal;
[0021] Among them, single mixed coal blendin...
PUM
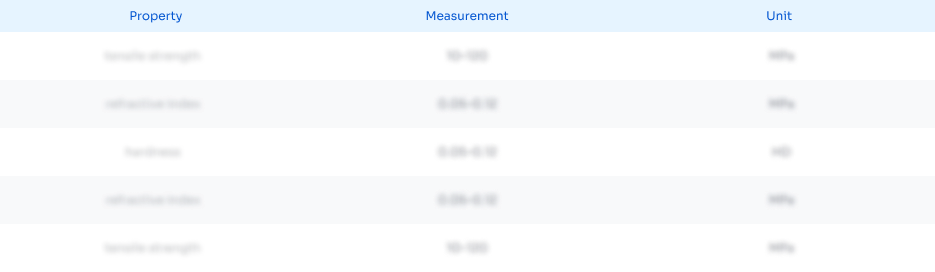
Abstract
Description
Claims
Application Information

- Generate Ideas
- Intellectual Property
- Life Sciences
- Materials
- Tech Scout
- Unparalleled Data Quality
- Higher Quality Content
- 60% Fewer Hallucinations
Browse by: Latest US Patents, China's latest patents, Technical Efficacy Thesaurus, Application Domain, Technology Topic, Popular Technical Reports.
© 2025 PatSnap. All rights reserved.Legal|Privacy policy|Modern Slavery Act Transparency Statement|Sitemap|About US| Contact US: help@patsnap.com