Standard knot jacking device and construction method for continuously and automatically jacking standard knots thereof
A jacking device and standard section technology, applied in the direction of lifting devices, etc., can solve the problems of increased total weight of steel structures, large construction site occupation, increased installation workload, etc., to achieve less auxiliary equipment, easy on-site assembly, and reduced installation work volume effect
- Summary
- Abstract
- Description
- Claims
- Application Information
AI Technical Summary
Problems solved by technology
Method used
Image
Examples
Embodiment 1
[0084] A jacking device for a standard section, including a sleeve frame 1, 2 transfer beams 2, 2 load-bearing beams 3, 4 transfer beam jacks 4, 4 luffing jacks 5, 4 jacking jacks 6, and a feed platform 7. Guide rail 8, 1 feed jack 9 and base 10 (see figure 1 ,figure 2);
[0085] The frame 1 that plays a guiding and stabilizing role during the jacking process and provides load transfer support is a steel frame welded by seamless steel tubes, consisting of upper and lower layers of square steel frames, connected by high-strength bolts, in the middle of the upper layer Two conversion beam installation beams 101 with a rectangular cross section are welded symmetrically on the part, and an extension beam 102 with a circular cross section for installing the luffing jack is arranged in the middle part of the lower layer of the sleeve frame. There is a rib 103 (see image 3 );
[0086] The base 10 is a square base that is welded horizontally and vertically by steel plates and has...
Embodiment 2
[0098] A construction method for automatic jacking of a standard section steel frame, which uses the standard section jacking device and an automatic control system described in Embodiment 1 to realize the automatic jacking of a standard section steel frame, and includes the following steps:
[0099] A. Install standard section steel frame jacking device:
[0100] Assemble the standard section steel frame jacking device and place it on the existing load-bearing structure;
[0101] B. Hoisting the steel frames of the first two standard sections:
[0102] Use a crane to hoist the first and second standard section steel frames to the base in the sleeve frame and stack them up, and connect the two standard section steel frames with high-strength bolts;
[0103] C Preparations before the first jacking (see figure 1 ,figure 2):
[0104] Use the automatic control system to control the action of the jacking jack 6 and the luffing jack 5, adjust the position of the load-bearing bea...
PUM
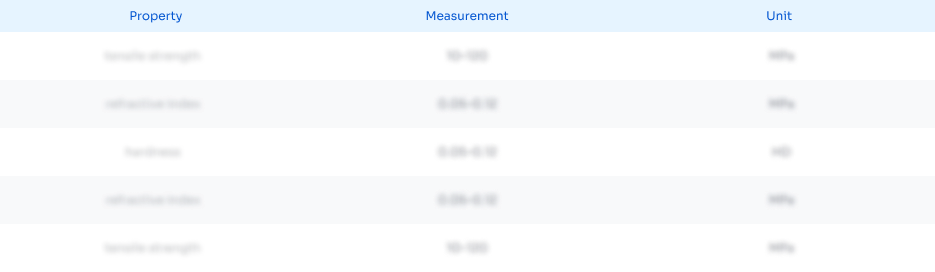
Abstract
Description
Claims
Application Information

- R&D
- Intellectual Property
- Life Sciences
- Materials
- Tech Scout
- Unparalleled Data Quality
- Higher Quality Content
- 60% Fewer Hallucinations
Browse by: Latest US Patents, China's latest patents, Technical Efficacy Thesaurus, Application Domain, Technology Topic, Popular Technical Reports.
© 2025 PatSnap. All rights reserved.Legal|Privacy policy|Modern Slavery Act Transparency Statement|Sitemap|About US| Contact US: help@patsnap.com