Low-temperature-resistance flame-retardant photodiffusion polycarbonate composite material and preparation method thereof
A polycarbonate and composite material technology, which is applied in the field of low temperature resistant flame retardant light diffusing polycarbonate composite materials and its preparation, can solve the problems of application limitation, impact resistance reduction, mechanical properties change, etc., and achieves high haze and Mechanical properties, excellent low temperature properties, the effect of improving low temperature properties
- Summary
- Abstract
- Description
- Claims
- Application Information
AI Technical Summary
Problems solved by technology
Method used
Examples
Embodiment 1
[0030] Embodiment 1, preparation of low temperature resistant flame retardant light diffusion polycarbonate composite material
[0031] The following components in parts by weight: 973 parts of PC model 2805, 4 parts of silicone microbead resin TSR-9002, 10 parts of potassium perfluorobutane sulfonate FRMB5010, 2 parts of antioxidant 168, 1 part Antioxidant 1076, 5 parts of long-chain fatty acid polyfunctional ester, 2 parts of light-stabilized 770, 2 parts of ultraviolet absorber UV234 and 1 part of toner are mixed in a high-speed mixer for 3 minutes, and put into the hopper of the twin-screw extruder , through melt extrusion and granulation, the granulation process is as follows: Twin-screw extruder zone 1 temperature 160-180°C, zone 2 temperature 220-240°C, zone 3 temperature 250-270°C, zone 4 temperature 250-270°C, The temperature of the fifth zone is 250-270°C, the temperature of the sixth zone is 250-270°C, the temperature of the seventh zone is 250-270°C, the temperatur...
Embodiment 2
[0032] Embodiment 2, preparation of low temperature resistant flame retardant light diffusion polycarbonate composite material
[0033] The following components in parts by weight: 823 parts of PC of type 2805, 150 parts of silicone copolymerized PCEXL1414T, 4 parts of silicone microbead resin TSR-9002, 10 parts of potassium perfluorobutane sulfonate FRMB5010, 2 parts Antioxidant 168, 1 part of antioxidant 1076, 5 parts of long-chain fatty acid polyfunctional esters, 2 parts of light stabilized 770, 2 parts of ultraviolet absorber UV234 and 1 part of toner were mixed in a high-speed mixer for 3 minutes, and put into double The feeding hopper of the screw extruder is granulated by melt extrusion. The granulation process is as follows: the temperature of the first zone of the twin-screw extruder is 160-180°C, the temperature of the second zone is 220-240°C, the temperature of the third zone is 250-270°C, and the temperature of the fourth zone is 250-270°C. Zone temperature 250-2...
Embodiment 3
[0034]Example 3, Preparation of low temperature resistant flame retardant light diffusing polycarbonate composite material
[0035] The following components in parts by weight: 723 parts of PC of type 2805, 250 parts of silicone copolymerized PCEXL1414T, 4 parts of silicone microbead resin TSR-9002, 10 parts of potassium perfluorobutane sulfonate FRMB5010, 2 parts Antioxidant 168, 1 part of antioxidant 1076, 5 parts of long-chain fatty acid polyfunctional esters, 2 parts of light stabilized 770, 2 parts of ultraviolet absorber UV234 and 1 part of toner were mixed in a high-speed mixer for 3 minutes, and put into double The feeding hopper of the screw extruder is granulated by melt extrusion. The granulation process is as follows: the temperature of the first zone of the twin-screw extruder is 160-180°C, the temperature of the second zone is 220-240°C, the temperature of the third zone is 250-270°C, and the temperature of the fourth zone is 250-270°C. Zone temperature 250-270℃,...
PUM
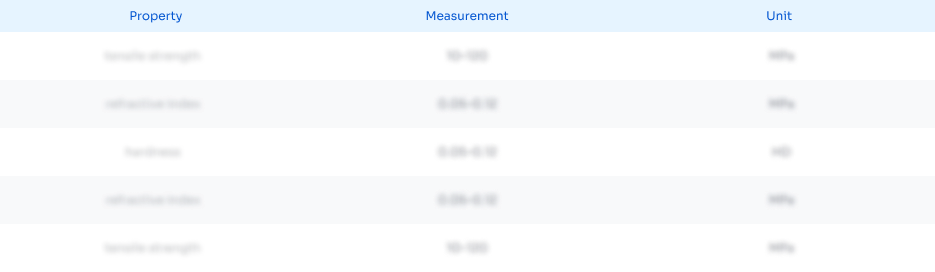
Abstract
Description
Claims
Application Information

- R&D Engineer
- R&D Manager
- IP Professional
- Industry Leading Data Capabilities
- Powerful AI technology
- Patent DNA Extraction
Browse by: Latest US Patents, China's latest patents, Technical Efficacy Thesaurus, Application Domain, Technology Topic, Popular Technical Reports.
© 2024 PatSnap. All rights reserved.Legal|Privacy policy|Modern Slavery Act Transparency Statement|Sitemap|About US| Contact US: help@patsnap.com