PDFF-based AC servo driver control parameter self-tuning method
A technology of controlling parameters and AC servo, applied in the direction of electric controllers, controllers with specific characteristics, etc., can solve the problems of speed loop control performance degradation, cumbersome control parameters, etc.
- Summary
- Abstract
- Description
- Claims
- Application Information
AI Technical Summary
Problems solved by technology
Method used
Image
Examples
Embodiment Construction
[0038] In order to make the objectives, technical solutions and advantages of the present invention clearer, the following further describes the present invention in detail with reference to the accompanying drawings and embodiments. It should be understood that the specific embodiments described herein are only used to explain the present invention, but not to limit the present invention. In addition, the technical features involved in the various embodiments of the present invention described below can be combined with each other as long as they do not conflict with each other.
[0039] The AC servo drive generally consists of three control loops: position loop, speed loop and current loop. The function of the current loop is to improve the rapid response capability of the system and suppress the interference inside the current loop. The function of the speed loop is to enhance the system's ability to resist external disturbances and improve the speed stability. The position l...
PUM
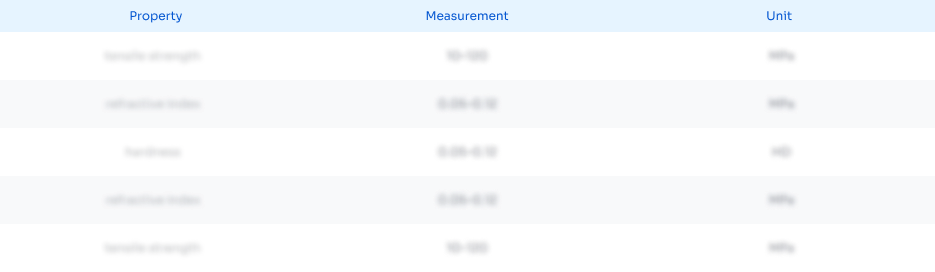
Abstract
Description
Claims
Application Information

- R&D
- Intellectual Property
- Life Sciences
- Materials
- Tech Scout
- Unparalleled Data Quality
- Higher Quality Content
- 60% Fewer Hallucinations
Browse by: Latest US Patents, China's latest patents, Technical Efficacy Thesaurus, Application Domain, Technology Topic, Popular Technical Reports.
© 2025 PatSnap. All rights reserved.Legal|Privacy policy|Modern Slavery Act Transparency Statement|Sitemap|About US| Contact US: help@patsnap.com