Method for obtaining and protecting piston position of aircraft electric brake actuator
A piston position and actuator technology, applied in the direction of brakes, brake transmissions, vehicle components, etc., can solve the problems of piston jamming, errors, and failure to guarantee the output of actuators, etc., to achieve the effect of avoiding jamming
- Summary
- Abstract
- Description
- Claims
- Application Information
AI Technical Summary
Problems solved by technology
Method used
Image
Examples
Embodiment Construction
[0035] Now in conjunction with embodiment, accompanying drawing, the present invention will be further described:
[0036] The structure of the electromechanical actuator in the aircraft electric braking system is as follows: figure 2 As shown, the actuator is mainly composed of a brake disc, a brake static disc, a piston, a ball screw, a reduction gear and a brushless DC motor. The number of pole pairs of the motor is 3, and its Hall position sensor is located at the rear end of the motor. .
[0037] The structure of the brushless DC motor drive controller is as follows: image 3 As shown, the main power part adopts a three-phase full-bridge inverter, the DC bus voltage is 160V, the power switch tube adopts N-channel power MOSFET, the switching frequency is set to 20kHz, and the driver chip adopts IR2130. The control unit is powered by 28V, uses TMS320F2812 as the main control chip, uses its on-chip analog-to-digital converter to collect the feedback signal of the pressure...
PUM
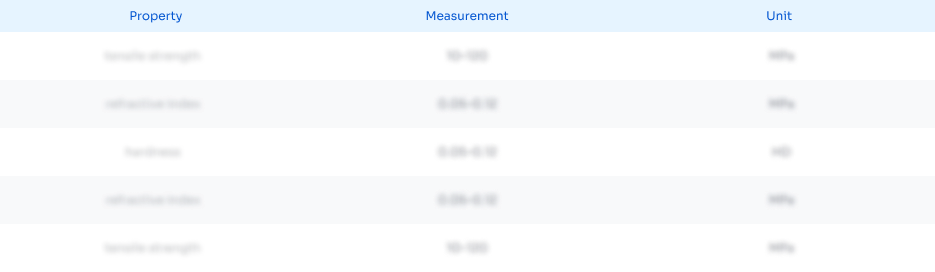
Abstract
Description
Claims
Application Information

- R&D
- Intellectual Property
- Life Sciences
- Materials
- Tech Scout
- Unparalleled Data Quality
- Higher Quality Content
- 60% Fewer Hallucinations
Browse by: Latest US Patents, China's latest patents, Technical Efficacy Thesaurus, Application Domain, Technology Topic, Popular Technical Reports.
© 2025 PatSnap. All rights reserved.Legal|Privacy policy|Modern Slavery Act Transparency Statement|Sitemap|About US| Contact US: help@patsnap.com