Preparation method of high-speed grinding fluid for bearing
A configuration method, grinding fluid technology, applied in the petroleum industry, lubricating composition, etc., can solve problems affecting the surface roughness of bearing workpieces, bearing surface burns, surface cracks, etc., to reduce temperature, improve grinding wheel durability, cooling good sex effect
- Summary
- Abstract
- Description
- Claims
- Application Information
AI Technical Summary
Problems solved by technology
Method used
Examples
Embodiment 1
[0063] Embodiment 1: 12% organic acid triethanolamine, 7% boric acid ester, 8% OP-10 and 4.5% oleic acid triethanolamine are added in the reactor, stir evenly; 0.5% sodium molybdate Add it to 10% distilled water, heat to 70-80°C, stir for 30 minutes, and add the fully dissolved solution to the reactor; add 1% fungicide and 0.5% defoamer to the reactor and stir evenly; Add 56.5% distilled water, stir evenly, and use pH test paper to test the pH value to reach the pH range of qualified high-speed grinding fluid, that is, configure qualified high-speed grinding fluid.
Embodiment 2
[0064] Embodiment 2: Add 11.5% organic acid triethanolamine, 8% boric acid ester, 7% OP-10 and 5% oleic acid triethanolamine to the reactor, stir well; add 0.8% sodium molybdate Add it to 10% distilled water, heat to 70-80°C, stir for 30 minutes, and add the fully dissolved solution to the reactor; add 1% fungicide and 0.5% defoamer to the reactor and stir evenly; Add 56.2% distilled water, use PH test paper to test the PH value, add 0.04% sodium carbonate and stir evenly, and use the PH test paper to test the PH value again to reach the pH range of qualified high-speed grinding fluid, that is, to configure qualified high-speed grinding fluid .
Embodiment 3
[0065] Embodiment 3: 10% organic acid triethanolamine, 9% boric acid ester, 6% OP-10 and 6% oleic acid triethanolamine are added in the reaction kettle, stir evenly; 1.1% sodium molybdate Add it to 10% distilled water, heat to 70-80°C, stir for 30 minutes, and add the fully dissolved solution to the reactor; add 1% fungicide and 0.5% defoamer to the reactor and stir evenly; Add 56.37% distilled water, use PH test paper to test the PH value, add 0.03% sodium carbonate and stir evenly, and use the PH test paper to test the PH value again to reach the pH range of qualified high-speed grinding fluid, that is, to configure qualified high-speed grinding fluid liquid.
PUM
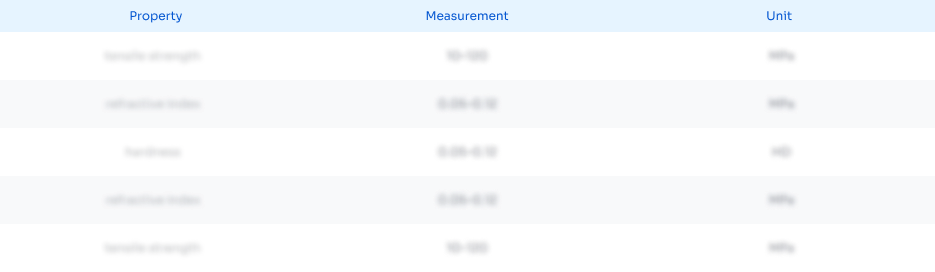
Abstract
Description
Claims
Application Information

- R&D
- Intellectual Property
- Life Sciences
- Materials
- Tech Scout
- Unparalleled Data Quality
- Higher Quality Content
- 60% Fewer Hallucinations
Browse by: Latest US Patents, China's latest patents, Technical Efficacy Thesaurus, Application Domain, Technology Topic, Popular Technical Reports.
© 2025 PatSnap. All rights reserved.Legal|Privacy policy|Modern Slavery Act Transparency Statement|Sitemap|About US| Contact US: help@patsnap.com