Deep extraction coking treatment process of oil-containing sludge
A treatment process and technology for sludge, applied in sludge treatment, water/sludge/sewage treatment, dehydration/drying/concentrated sludge treatment, etc., can solve the use limitation, affect the coke volatile content and ash index, and affect the petroleum Coke quality and other issues, to reduce impact, reduce volume and quality, and achieve the effect of recycling and utilization
- Summary
- Abstract
- Description
- Claims
- Application Information
AI Technical Summary
Problems solved by technology
Method used
Examples
Embodiment 1
[0034] The extraction solvent formula is as follows: the main agent of the extraction solvent is distillate oil with a boiling range of naphtha 110-135°C, accounting for 95%; the auxiliary agent is distillate oil with a boiling range of 140-150°C, accounting for 4%; Distillate oil with a range of 80-100°C, accounting for 1%, constitutes a composite extractant. After mechanical dehydration, the oily sludge produced by a refinery sewage treatment plant has a water content of 76.6wt%, an oil content of 17.6%, and a solid content of 5.1%. Send the sludge into the squeezer, the squeezing temperature is 25°C, and the pressure is 28MPa. After squeezing for 30 minutes, the water content of the generated mud cake is 18.6%, and the oil content is 59.6%. It is mixed with the composite extraction solvent at a ratio of 1:10 for 30 minutes (temperature 30°C), after the extraction is finished, the solid-liquid mixture is sent to the centrifugal separator, the separated liquid phase is sent t...
Embodiment 2
[0038] The formula of the extraction solvent is as follows: the main agent of the extraction solvent is distillate oil with a boiling range of naphtha 110-135°C, accounting for 90%; the auxiliary agent is distillate oil with a boiling range of 140-150°C, accounting for 8%; Distillate oil with a range of 80-100°C, accounting for 2%, constitutes a composite extractant. After mechanical dehydration, the oily sludge produced by an oil refinery sewage treatment plant has a water content of 79.5wt%, an oil content of 16.7%, and a solid content of 4.7%. After the sludge is squeezed (pressing temperature is 25°C, pressure is 26MPa, squeezed for 20 minutes, the water content of the resulting mud cake is 23.4%, oil content is 52.6%, and it is mixed and extracted with the composite extraction solvent at a ratio of 1:8 (temperature is 70°C , time 15min), after the extraction is finished, the solid-liquid mixture is sent to the centrifugal separator, the separated liquid phase is sent to t...
Embodiment 3
[0042] The formula of the extraction solvent is as follows: the main agent of the extraction solvent is distillate oil with a boiling range of 110-135°C of naphtha, accounting for 92%; the auxiliary agent is selected from distillate oil with a boiling range of 140-150°C, accounting for 8%; agent. After mechanical dehydration, the oily sludge produced by a refinery sewage treatment plant has a water content of 79.5wt%, an oil content of 16.7%, and a solid content of 4.7%. After the sludge is squeezed (pressing temperature is 25°C, pressure is 29MPa, and pressing is 40min), the water content of the sludge cake is 16.2%, and the oil content is 59.8%. , time 30min), after the extraction is finished, the solid-liquid mixture is sent to the centrifugal separator, the separated liquid phase is sent to the coking device, and the solid phase is sent to the rotary kiln evaporator, at a temperature of 160°C and a pressure of 60kpa (absolute After evaporating for 72 minutes under pressur...
PUM
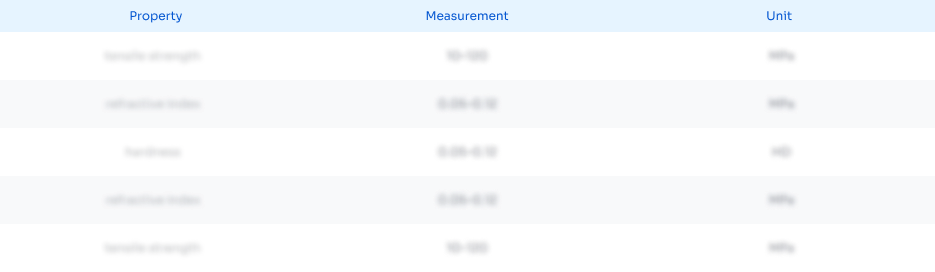
Abstract
Description
Claims
Application Information

- Generate Ideas
- Intellectual Property
- Life Sciences
- Materials
- Tech Scout
- Unparalleled Data Quality
- Higher Quality Content
- 60% Fewer Hallucinations
Browse by: Latest US Patents, China's latest patents, Technical Efficacy Thesaurus, Application Domain, Technology Topic, Popular Technical Reports.
© 2025 PatSnap. All rights reserved.Legal|Privacy policy|Modern Slavery Act Transparency Statement|Sitemap|About US| Contact US: help@patsnap.com