Treatment method of porous carbon carrier for noble metal catalysts
A precious metal catalyst and treatment method technology, applied in catalyst carriers, chemical instruments and methods, physical/chemical process catalysts, etc., can solve problems such as less treatment, and achieve the effects of simple method, improved surface properties, and low cost
- Summary
- Abstract
- Description
- Claims
- Application Information
AI Technical Summary
Problems solved by technology
Method used
Image
Examples
Embodiment 1
[0025] Carbon nanotube processing method
[0026] Add 100 grams of carbon nanotubes into the three-necked flask, control the temperature at 20 degrees, slowly add 200 milliliters of concentrated nitric acid (which is also an oxidant) under stirring, control the temperature to 120 degrees, reflux the concentrated nitric acid for 12 hours, and then centrifuge to obtain the product. The product was washed with deionized water, dried at 100°C, and calcined at 500°C for 3 hours in a hydrogen-argon mixed gas (5% hydrogen) to obtain the treated product. figure 1 It is the SEM photo of the product.
Embodiment 2
[0028] Porous carbon treatment method
[0029] (1) Preparation method of oxidized porous carbon
[0030] Add 120 grams of NaNO to the three-neck flask 3 , slowly add 1000 ml concentrated H under stirring 2 SO 4 , heated to 40 degrees and stirred until dissolved; cooled the acid solution with an ice-water bath, then added 240 grams of porous carbon into the acid solution, and stirred for 0.5 hours; then slowly added KMnO in an ice-water bath 4 After the addition, react for 5-10 minutes until the heat release stops, remove the ice-water bath, use an oil bath to heat the reaction solution to about 40 degrees, and react for 2-4 hours under stirring. After the reaction is over, switch to a condensing device, turn on the circulating water, slowly add 2000 ml of deionized water, heat while adding deionized water to keep the temperature at about 98-100°C, and react for 4 hours. After the reaction, the oil bath was removed, and deionized water was added to dilute the solution, then...
PUM
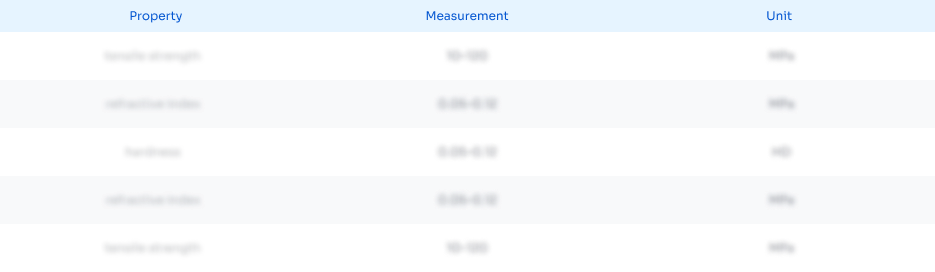
Abstract
Description
Claims
Application Information

- R&D
- Intellectual Property
- Life Sciences
- Materials
- Tech Scout
- Unparalleled Data Quality
- Higher Quality Content
- 60% Fewer Hallucinations
Browse by: Latest US Patents, China's latest patents, Technical Efficacy Thesaurus, Application Domain, Technology Topic, Popular Technical Reports.
© 2025 PatSnap. All rights reserved.Legal|Privacy policy|Modern Slavery Act Transparency Statement|Sitemap|About US| Contact US: help@patsnap.com