One bath process desizing and dyeing technology of viscose leather base cloth
A viscose leather base fabric and desizing technology, which is applied in dyeing, biochemical fiber treatment, textiles and papermaking, etc., can solve the problems of high labor cost, water, electricity, steam consumption, and large sewage discharge, and improve dyeing stability , Water consumption reduction, coal consumption saving effect
- Summary
- Abstract
- Description
- Claims
- Application Information
AI Technical Summary
Problems solved by technology
Method used
Examples
Embodiment 1
[0023] The one-bath desizing and dyeing process of the viscose leather base cloth of the present invention, when producing 0.5 sticky sword green brown varieties, according to the color metering consumption of reactive dyes, drop into the dyeing machine water bath and account for 2.5% of the weight of the viscose gray cloth. Desizing enzyme, anionic surfactant accounting for 1% of the weight of viscose gray cloth, put the medium temperature reactive dye into the prepared viscose leather base cloth normal temperature jigger at 60°C (the weight of the gray cloth is equal to the water in the water bath The specific gravity of the dosage is 1:1.5), and the machine is driven to 60°C for 4 passes, and soda ash is added to fix the color in the last 2 passes to complete the one-bath desizing and dyeing process.
[0024] Wherein, the composite desizing enzyme is prepared from the following components by weight percentage: 40% wide temperature starch desizing enzyme, 25% refining enzyme ...
Embodiment 2
[0028] The one-bath desizing and dyeing process of the viscose leather base cloth of the present invention, when producing the 0.2 sticky sword left oblique extra deep black variety, the consumption of sulfur dyes is measured according to the color, and the viscose gray cloth weight 2 is put into the jigger water bath. % multifunctional pretreatment agent, anionic surfactant accounting for 1.5% of the weight of viscose gray cloth, put the sulfur dye into the prepared viscose leather base cloth normal temperature jigger at 75°C (the weight of the gray cloth is the same as that in the water bath The proportion of water used is 1:1.5), and the machine is driven to 75°C for 2 passes, and then the temperature is raised to 98°C and maintained for 3 passes to complete the desizing and dyeing one-bath process.
[0029] Wherein, the multifunctional pretreatment agent includes the following weight percentage combination: 45% cotton cleaning enzyme, 20% refining enzyme and 25% water.
[...
PUM
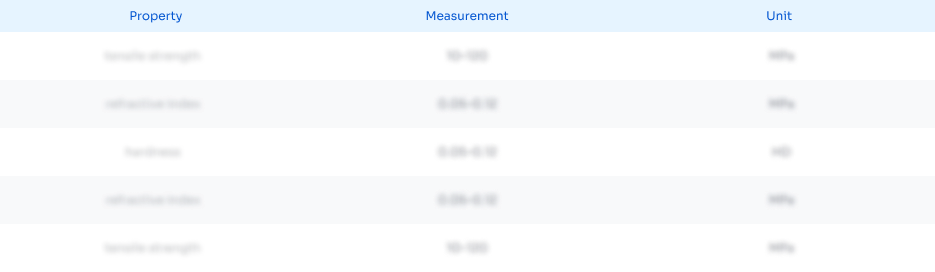
Abstract
Description
Claims
Application Information

- R&D Engineer
- R&D Manager
- IP Professional
- Industry Leading Data Capabilities
- Powerful AI technology
- Patent DNA Extraction
Browse by: Latest US Patents, China's latest patents, Technical Efficacy Thesaurus, Application Domain, Technology Topic, Popular Technical Reports.
© 2024 PatSnap. All rights reserved.Legal|Privacy policy|Modern Slavery Act Transparency Statement|Sitemap|About US| Contact US: help@patsnap.com