Titanium-based composite anode for manganese electrolysis and preparation method of titanium-based composite anode
A composite anode and manganese electrolysis technology, applied in the field of electrochemistry, can solve the problems of anode by-products containing lead, difficult to reuse, and high anode potential, and achieve the effects of large capacity, difficult passivation, and high cycle life
- Summary
- Abstract
- Description
- Claims
- Application Information
AI Technical Summary
Problems solved by technology
Method used
Image
Examples
Embodiment 1
[0026] -320 mesh pure titanium powder, polyvinyl alcohol, hydrogen peroxide, and deionized water are formulated into a slurry at a mass ratio of 1:0.1:0.2:0.7, coated on a 0.15mm 60 mesh titanium screen, and fired at 60°C. Soak and dry, and then sinter in a vacuum furnace at 1300°C for 2h to obtain a titanium foam matrix reinforced with titanium mesh. The titanium mesh-reinforced foamed titanium substrate was heated to boiling for 2 h with oxalic acid solution with a mass fraction of 15% for mild etching, and the RuCl 3 ·3H 2 O, H 2 IrCl 6 ·6H 2 O is dissolved in hydrochloric acid and ethanol to prepare a coating solution according to the ratio of substances of 3:1, and is coated on the surface of the foamed titanium substrate, dried at 100°C for 15 minutes, then oxidized at 500°C for 10 minutes, after cooling, remove loose matter on the surface, and then The coating was repeated 10 times, and finally the sample was calcined at 500°C for 2 hours to convert chlorides into c...
Embodiment 2
[0029]-320 mesh pure titanium powder and polyvinyl alcohol, hydrogen peroxide, and deionized water are made into a slurry at a mass ratio of 1:0.05:0.3:0.5, and coated on a 40 mesh titanium screen with a wire diameter of 0.25mm. It was foamed and dried at ℃, and then sintered at 1250℃ for 2h in a vacuum furnace to obtain a titanium foam matrix reinforced with titanium mesh. Using oxalic acid solution with a mass fraction of 15%, the titanium mesh-reinforced foamed titanium substrate was heated to boiling for 2 h for mild etching, and H 2 IrCl 6 ·6H 2 O, TaCl 5 Dissolve it in hydrochloric acid and ethanol to prepare a coating solution according to the ratio of the substance at 2:1, apply it on the surface of the foamed titanium substrate, dry it at 100°C for 15 minutes, then oxidize it at 500°C for 10 minutes, remove loose matter on the surface after cooling, and repeat After coating 15 times, the sample was calcined at 500°C for 1 hour to convert chlorides into correspondin...
Embodiment 3
[0032] -320 mesh pure titanium powder and polyvinyl alcohol, hydrogen peroxide, and deionized water are formulated into a slurry at a mass ratio of 1:0.2:0.2:0.6, coated on a 0.29mm 30 mesh titanium screen, and fired at 45°C. Soak and dry, and then sinter in a vacuum furnace at 1300°C for 2h to obtain a titanium foam matrix reinforced with titanium mesh. The titanium mesh-reinforced foamed titanium substrate was heated to boiling for 2 h with oxalic acid solution with a mass fraction of 15% for mild etching, and the RuCl 3 ·3H 2 O was dissolved in hydrochloric acid and ethanol to make a coating solution, coated on the surface of the foamed titanium substrate, dried at 100°C for 15 minutes, then oxidized at 500°C for 10 minutes, removed surface loose matter after cooling, and repeated coating 5 times, and finally the sample Calcined at 500°C for 1-2h to convert chlorides into corresponding oxides. Then with the composite material coated with the noble metal oxide coating as t...
PUM
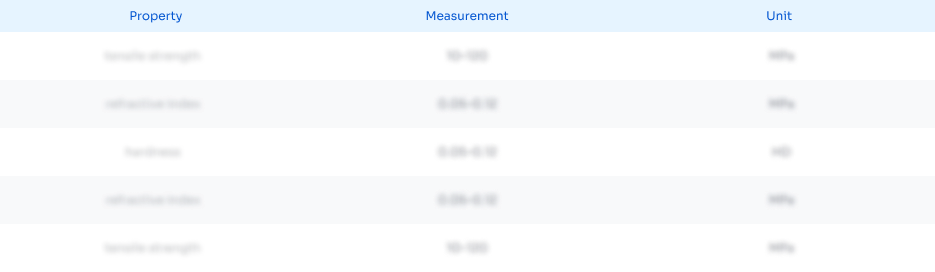
Abstract
Description
Claims
Application Information

- R&D
- Intellectual Property
- Life Sciences
- Materials
- Tech Scout
- Unparalleled Data Quality
- Higher Quality Content
- 60% Fewer Hallucinations
Browse by: Latest US Patents, China's latest patents, Technical Efficacy Thesaurus, Application Domain, Technology Topic, Popular Technical Reports.
© 2025 PatSnap. All rights reserved.Legal|Privacy policy|Modern Slavery Act Transparency Statement|Sitemap|About US| Contact US: help@patsnap.com