Preparation method of glufosinate
A technology of glufosinate-ammonium and compound, which is applied in the field of preparation of glufosinate-ammonium, can solve the problems of cumbersome reaction steps, harsh reaction conditions, and many waste acids, and achieve the effect of simple and quick operation, fewer reaction steps, and high yield
- Summary
- Abstract
- Description
- Claims
- Application Information
AI Technical Summary
Problems solved by technology
Method used
Image
Examples
Embodiment 1
[0025] Step (1): Preparation of the compound shown in formula (II)
[0026] Add 4.9 g of crushed sodium cyanide and 50 ml of dried chloroform into a 500 ml dry three-necked flask, stir and heat to 50°C, and slowly add 13.4 g of the compound represented by formula (I) and 67 ml of dried The mixed solution of chloroform, the dropping temperature is controlled at 50°C-60°C, after the dropwise addition, the heat preservation reaction is carried out for 2 hours, after the reaction is completed, the solvent chloroform is distilled off under reduced pressure, cooled and filtered, and dried to obtain 18.3 grams of white solid powder , which is the compound represented by formula (II).
[0027] Step (2): Preparation of the compound shown in formula (Ⅲ)
[0028] In a 250 ml three-necked flask, add 122 grams of 30% hydrochloric acid, stir, and then add 18.3 grams of the compound shown in formula (II). Add hydrogen chloride, stir and react at this temperature for about 1.5 hours, then h...
Embodiment 2
[0032] Step (1): Preparation of the compound shown in formula (II)
[0033] Add 6.8 g of crushed potassium cyanide and 50 ml of dried chloroform into a 500 ml dry three-necked flask, stir and heat to 60°C, and slowly add 18.5 g of the compound represented by formula (I) and 67 ml of dried For the mixed solution of chloroform, the dropwise addition temperature is controlled at 55°C-65°C. After the dropwise addition, the heat preservation reaction is carried out for 2 hours. After the reaction is completed, the solvent chloroform is distilled off under reduced pressure, cooled, filtered, and dried to obtain 25.3 grams of white solid powder, namely It is a compound represented by formula (II).
[0034] Step (2): Preparation of the compound shown in formula (Ⅲ)
[0035] In 250 milliliters of three ports, add 122 grams of 30% hydrochloric acid, stir, then add 25.3 grams of the compound shown in formula (II), after the addition is complete, the reaction system is rapidly reduced to...
Embodiment 3
[0039] Step (1): Preparation of the compound shown in formula (II)
[0040]Add 4.9 g of crushed sodium cyanide and 50 ml of dried dichloroethane into a 500 ml dry three-necked flask, stir and heat to 50°C, and slowly add 13.4 g of the compound represented by formula (I) and 67 Milliliters of dried dichloroethane mixed solution, the dropwise addition temperature is controlled at 50°C-60°C, after the dropwise addition, keep warm for 2 hours, after the reaction, the solvent dichloroethane is distilled off under reduced pressure, cooled and filtered, After drying, 17.5 g of white solid powder was obtained, which was the compound represented by formula (II).
[0041] Step (2): Preparation of the compound shown in formula (Ⅲ)
[0042] In a 250 ml three-neck flask, add 150 g of 30% phosphoric acid, stir, then add 17.5 g of the compound shown by formula (II), heat to 110°C, and react for 10 hours. Then the water was evaporated under reduced pressure, and evaporated to dryness as muc...
PUM
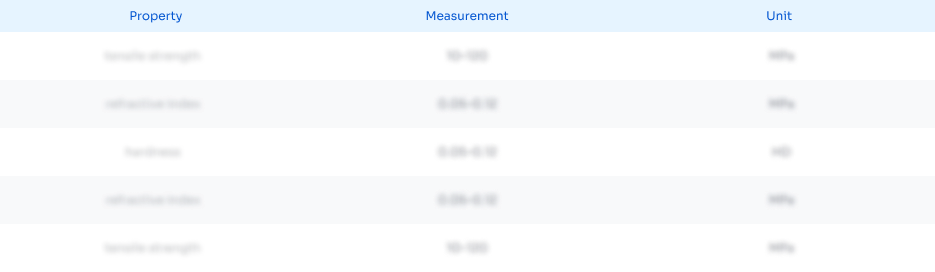
Abstract
Description
Claims
Application Information

- R&D
- Intellectual Property
- Life Sciences
- Materials
- Tech Scout
- Unparalleled Data Quality
- Higher Quality Content
- 60% Fewer Hallucinations
Browse by: Latest US Patents, China's latest patents, Technical Efficacy Thesaurus, Application Domain, Technology Topic, Popular Technical Reports.
© 2025 PatSnap. All rights reserved.Legal|Privacy policy|Modern Slavery Act Transparency Statement|Sitemap|About US| Contact US: help@patsnap.com