Universal grinding machine special for nuclear power bearing inner race machining
A technology for bearing inner rings and universal grinding machines, which is applied to grinding machines, metal processing equipment, and parts of grinding machine tools. It can solve problems such as cumbersome and complicated, high error rates, and increased scrapped workpieces, and achieve lower skill requirements, The effect of improving the adjustment accuracy
- Summary
- Abstract
- Description
- Claims
- Application Information
AI Technical Summary
Problems solved by technology
Method used
Image
Examples
Embodiment Construction
[0043] A special universal grinding machine for processing the inner ring of a nuclear power bearing, including a machine base 1, a bed 2, a hydraulic system 13, an electric control system 3, a servo system 4, and an electric spindle 5, a spindle lifting mechanism 6, a workpiece shaft 7, and a grinding wheel dressing Device, workpiece translation mechanism 8, support assembly 200, mechanical arm 300, magnetic pole 400, grinding wheel 9, cutting fluid circulation system 500, nuclear power bearing inner ring 1007;
[0044] The electric spindle 5 and the spindle lifting mechanism 6 are two sets, which are respectively installed on the upper part of the working translation mechanism 8. Each set of electric spindle 5 works independently and moves up and down through the spindle lifting mechanism 6. The lower end of the electric spindle 5 is equipped with a grinding wheel 9, and the electric spindle drives The grinding wheel 9 rotates;
[0045] The workpiece shaft 7 is arranged on t...
PUM
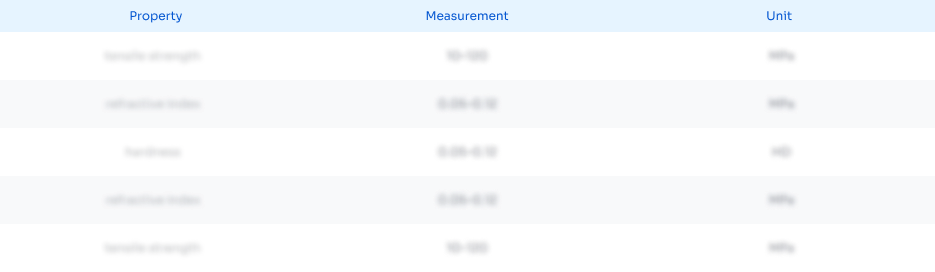
Abstract
Description
Claims
Application Information

- R&D
- Intellectual Property
- Life Sciences
- Materials
- Tech Scout
- Unparalleled Data Quality
- Higher Quality Content
- 60% Fewer Hallucinations
Browse by: Latest US Patents, China's latest patents, Technical Efficacy Thesaurus, Application Domain, Technology Topic, Popular Technical Reports.
© 2025 PatSnap. All rights reserved.Legal|Privacy policy|Modern Slavery Act Transparency Statement|Sitemap|About US| Contact US: help@patsnap.com