Cavity filter, duplexer, combiner and transmission zero frequency debugging method for cavity filter
A cavity filter and cavity technology, applied in the field of communication, can solve the problems of high filter production cost, high purchase price, increased material cost, etc., and achieve the effect of reducing the cost of raw material procurement, reducing the probability of errors, and saving assembly man-hours.
- Summary
- Abstract
- Description
- Claims
- Application Information
AI Technical Summary
Problems solved by technology
Method used
Image
Examples
Embodiment 1
[0028] Please refer to image 3 , Figure 4 As shown, Embodiment 1 of the present invention provides a cavity filter 1 , including: a cavity 10 , resonators 11 , 12 , 13 and a coupling jumper 2 .
[0029] The resonators 11, 12, and 13 are placed in the cavity 10, and are arranged in a right triangle in this embodiment. The resonators 11 and 13 are respectively located at both ends of the hypotenuse of the right triangle, and are respectively connected to signal input and output terminals to form a resonator 11. →12→13 for the main transmission path, and the resonator 11→13 for the transmission secondary path.
[0030] The coupling jumper 2 further includes a coupling part 21 and an assembly part 22 . The length of the coupling part 21 is λ / 4, where λ represents the wavelength corresponding to the transmission zero frequency required by design. The open circuit of the λ / 4 wavelength terminal is equivalent to the inductance of the inner conductor and the series connection of ...
Embodiment 2
[0037] For the comb cavity filter, the resonators are arranged in a "one" shape, which cannot be implemented in the coupling probe method in the prior art. For this, please refer to Figure 6 , Figure 7 As shown, Embodiment 2 of the present invention provides a cavity filter 6 , including: a cavity 60 , resonators 61 , 62 , 63 and coupling jumpers 7 .
[0038] The resonators 61, 62, 63 are placed in the cavity 60, arranged in a "one" shape in this embodiment, and the resonators 61 and 63 are respectively located at both ends of the "one" shape, and connected to the signal input and output terminals to form The transmission main path of the resonator 61→62→63, and the transmission secondary path of the resonator 61→63.
[0039] The coupling jumper 2 further includes a coupling part 21 and an assembly part 22 . The length of the coupling part 21 is λ / 4, where λ represents the wavelength corresponding to the transmission zero frequency required by design. Same as the first e...
Embodiment 3
[0047] In the cavity filters provided by Embodiments 1 and 2 of the present invention, capacitive cross-coupling is introduced into the transmission secondary path, so that a transmission zero point is generated on the left side (low end) of the transmission passband of the cavity filter. Although the transmission zero frequency required by the design can be basically achieved by controlling the length of the coupling part (21, 71) of the coupling jumper (2, 7), but considering the inevitable errors generated in the process of production, processing and assembly, for To more accurately make the transmission zero frequency meet the design requirements, Embodiment 3 of the present invention provides a transmission zero frequency debugging method, including:
[0048] Judging the difference between the actual transmission zero frequency and the designed transmission zero frequency;
[0049] Move the actual transmission zero frequency to the right by raising the height of the jumpe...
PUM
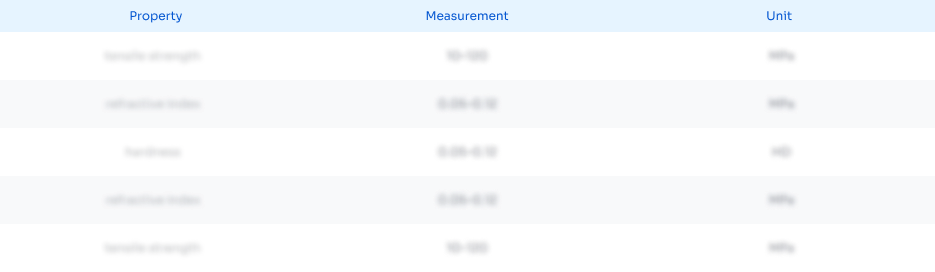
Abstract
Description
Claims
Application Information

- R&D
- Intellectual Property
- Life Sciences
- Materials
- Tech Scout
- Unparalleled Data Quality
- Higher Quality Content
- 60% Fewer Hallucinations
Browse by: Latest US Patents, China's latest patents, Technical Efficacy Thesaurus, Application Domain, Technology Topic, Popular Technical Reports.
© 2025 PatSnap. All rights reserved.Legal|Privacy policy|Modern Slavery Act Transparency Statement|Sitemap|About US| Contact US: help@patsnap.com