Manufacturing method of high-yield non-bonding prestress steel bar
A prestressed steel bar and a manufacturing method are applied in the manufacturing field of metal products, which can solve the problems of no insulating protective layer, unsatisfactory insulating effect, complicated construction procedures, etc., so as to avoid excessive corrosion rate, avoid intergranular corrosion and The effect of pitting exceeding the standard and ensuring the ferrite content
- Summary
- Abstract
- Description
- Claims
- Application Information
AI Technical Summary
Problems solved by technology
Method used
Examples
Embodiment 1
[0031] This embodiment provides a method for manufacturing high-yield unbonded prestressed steel rods, comprising the following steps:
[0032] Step 1: Use high manganese steel as the base material, add the base material and alloy into the furnace for preliminary smelting to obtain billets, the temperature of the preliminary smelting is 1250-1300°C, keep warm for 0.5-0.75h after smelting, the amount of alloy added is 2-4% of the weight of the material, the alloy includes the following components by mass percentage: carbon: 0.55%, silicon: 1%, manganese: 0.8%, chromium: 1.15%, molybdenum: 0.13%, tungsten: 0.07, phosphorus: 0.025 %, sulfur: 0.0075%, vanadium: 0.035%, aluminum: 0.017%, niobium: 0.25%, 0-0.07% residual elements, the rest is Fe, and vanadium is added by adding ferrovanadium nitride;
[0033] Step 2: Water-cool the blank obtained in step 1 to room temperature at a cooling rate of 18-20°C / s, and then temper. The tempering temperature is 1450-1500°C, and the tempering...
Embodiment 2
[0042] This embodiment provides a method for manufacturing high-yield unbonded prestressed steel rods, comprising the following steps:
[0043] Step 1: Use high manganese steel as the base material, add the base material and alloy into the furnace for preliminary smelting to obtain billets, the temperature of the preliminary smelting is 1250-1300°C, keep warm for 0.5-0.75h after smelting, the amount of alloy added is 2-4% of the weight of the material, the alloy includes the following components by mass percentage: carbon: 0.6%, silicon: 0.9%, manganese: 0.77%, chromium: 1.16%, molybdenum: 0.24%, tungsten: 0.05, phosphorus: 0.025 %, sulfur: 0.0075%, vanadium: 0.025%, aluminum: 0.03%, niobium: 0.19%, 0-0.07% residual elements, the rest is Fe, and vanadium is added by adding ferrovanadium nitride;
[0044] Step 2: Water-cool the blank obtained in step 1 to room temperature at a cooling rate of 18-20°C / s, and then temper. The tempering temperature is 1450-1500°C, and the temperin...
Embodiment 3
[0053] This embodiment provides a method for manufacturing high-yield unbonded prestressed steel rods, comprising the following steps:
[0054] Step 1: Use high manganese steel as the base material, add the base material and alloy into the furnace for preliminary smelting to obtain billets, the temperature of the preliminary smelting is 1250-1300°C, keep warm for 0.5-0.75h after smelting, the amount of alloy added is 2-4% of the weight of the material, the alloy includes the following components by mass percentage: carbon: 0.65%, silicon: 1.1%, manganese: 0.75%, chromium: 1.07%, molybdenum: 0.19%, tungsten: 0.03, phosphorus: 0.025 %, sulfur: 0.0075%, vanadium: 0.02%, aluminum: 0.01%, niobium: 0.17%, 0-0.07% residual elements, the rest is Fe, and vanadium is added by adding ferrovanadium nitride;
[0055] Step 2: Water-cool the blank obtained in step 1 to room temperature at a cooling rate of 18-20°C / s, and then temper. The tempering temperature is 1450-1500°C, and the temperin...
PUM
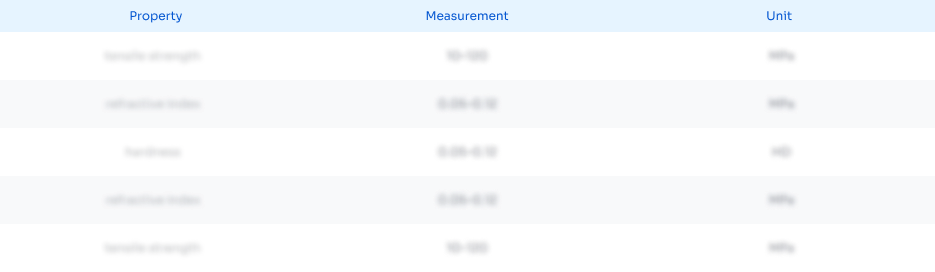
Abstract
Description
Claims
Application Information

- R&D
- Intellectual Property
- Life Sciences
- Materials
- Tech Scout
- Unparalleled Data Quality
- Higher Quality Content
- 60% Fewer Hallucinations
Browse by: Latest US Patents, China's latest patents, Technical Efficacy Thesaurus, Application Domain, Technology Topic, Popular Technical Reports.
© 2025 PatSnap. All rights reserved.Legal|Privacy policy|Modern Slavery Act Transparency Statement|Sitemap|About US| Contact US: help@patsnap.com