Method for preparing carbon nanotube film
A carbon nanotube film and carbon nanotube technology are applied in the field of carbon nanotube film preparation, which can solve the problems of pattern defects, small beam size, and long time consumption.
- Summary
- Abstract
- Description
- Claims
- Application Information
AI Technical Summary
Problems solved by technology
Method used
Image
Examples
Embodiment approach
[0048] Embodiments are not limited to etch paste application methods or photoresist methods, and if some methods are melting away the etch target area E in the top adhesive layer 140, CNT coating layer 130, and base adhesive layer 120 ), then this method is also applicable to the concept of the present invention.
[0049] According to an exemplary embodiment, the CNT coating layer 130 is patterned by wet etching. Therefore, conventional wet etching equipment for patterning electrodes such as ITO may be applicable. Moreover, it can be etched quickly, and can form a fine pattern width.
[0050] Figure 7 is a flowchart illustrating a method of preparing a carbon nanotube film according to another exemplary embodiment of the present inventive concept. like Figure 7 As shown, the method S200 for preparing a carbon nanotube film includes, forming a CNT coating S210 comprising carbon nanotubes on a substrate, forming a wet-etched top adhesive layer S220 on the CNT coating, and ...
PUM
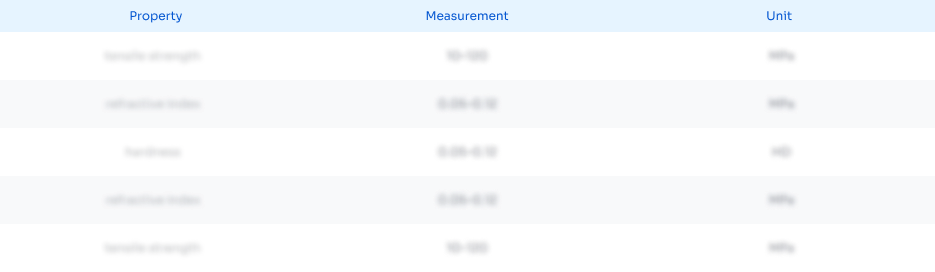
Abstract
Description
Claims
Application Information

- R&D
- Intellectual Property
- Life Sciences
- Materials
- Tech Scout
- Unparalleled Data Quality
- Higher Quality Content
- 60% Fewer Hallucinations
Browse by: Latest US Patents, China's latest patents, Technical Efficacy Thesaurus, Application Domain, Technology Topic, Popular Technical Reports.
© 2025 PatSnap. All rights reserved.Legal|Privacy policy|Modern Slavery Act Transparency Statement|Sitemap|About US| Contact US: help@patsnap.com