Back contact crystalline silicon battery, treatment method for non-illuminated surface of back contact crystalline silicon battery and preparation method for back contact crystalline silicon battery
A crystalline silicon cell and processing method technology, applied in circuits, photovoltaic power generation, electrical components, etc., can solve the problem of low photoelectric conversion efficiency of crystalline silicon cells, and achieve the effects of increasing photoelectric conversion efficiency, enhancing physical strength, and reducing recombination rate.
- Summary
- Abstract
- Description
- Claims
- Application Information
AI Technical Summary
Problems solved by technology
Method used
Image
Examples
Embodiment 1
[0056] This embodiment provides a rear contact silicon cell, such as Figure 2-4 As shown, it includes a silicon substrate 100. The silicon substrate 100 has a light-receiving surface and a non-light-receiving surface. On the non-light-receiving surface, there are a P-type region converging conductive strip 108 and an N-type region converging conductive strip 112, which are formed into a P-N-P-N type Arrangement structure, the P-type zone bussing conductive strip 108 is connected to the positive metal electrode 110, the N-type zone bussing conductive strip 112 is connected to the negative electrode metal electrode, covering the P-type zone bussing conductive strip 108 and the N-type zone The bus conductive strip 112 is arranged on the five-layer Bragg reflective layer 200 on the non-light-receiving surface. The Bragg reflective layer 200 is arranged along the thickness direction of the crystalline silicon cell, and each layer of the Bragg reflective layer 200 includes a first ...
Embodiment 2
[0060] This embodiment provides a rear contact crystalline silicon cell, which is a modification based on Embodiment 1. The difference is that in this embodiment, the light with a central wavelength λ=600nm is taken as the target reflected light, and the formula d1=d2 =1 / 8λ is calculated to obtain d1=d2=75nm, according to this data, 5 layers of the above-mentioned Bragg reflection layer 200 are deposited on the non-light-receiving surface, and the data obtained from the test are as follows Image 6 As shown, the maximum reflectance 302 of light in the wavelength range of 400-800nm is 65%, the average reflectance 300 is 30%, and Figure 5 The data in is not much different, but the reflection effect is greatly enhanced compared with the reflection effect of the existing passivation layer.
[0061] As a modification to this embodiment, the Bragg reflection layer 200 may be provided with 2-8 layers, all of which can achieve the purpose of the invention.
Embodiment 3
[0063] This embodiment provides a rear contact silicon cell, which is a modification based on Embodiment 1, the difference is that the first material in this embodiment is SiO 2 , the thickness of the first Bragg reflection film formed by it is d1, and the second material is TiO 2 , the thickness of the second Bragg reflection film formed by it is d2, where SiO 2 The refractive index n 1 =1.46,TiO 2 The refractive index n 2 =2.35.
[0064] Take the center wavelength as λ 1 =500nm and λ 2 =800nm light reflects light for two targets, and passes the formula d1=(2λ 1 -λ 2 ) / (2n 1 ), d2=(λ 2 -λ 1 ) / (2n 2 ) are calculated respectively to obtain d1=68.2nm, d2=78.9nm, according to this data, 5 layers of the above-mentioned Bragg reflection layer 200 are deposited on the non-light-receiving surface, and the data obtained by the test are as follows Figure 7 As shown, the maximum reflectance 302 for light in the wavelength range of 400-800nm is 93%, and the average refle...
PUM
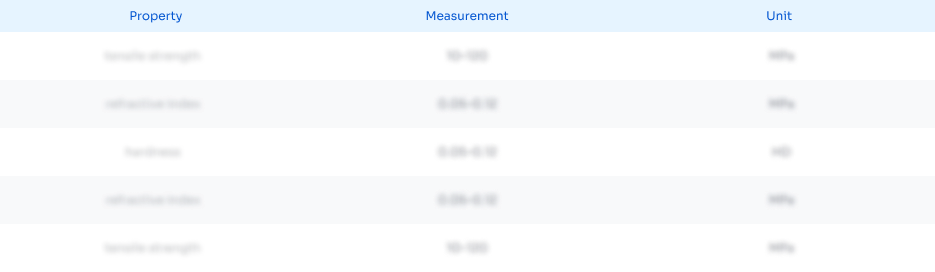
Abstract
Description
Claims
Application Information

- R&D
- Intellectual Property
- Life Sciences
- Materials
- Tech Scout
- Unparalleled Data Quality
- Higher Quality Content
- 60% Fewer Hallucinations
Browse by: Latest US Patents, China's latest patents, Technical Efficacy Thesaurus, Application Domain, Technology Topic, Popular Technical Reports.
© 2025 PatSnap. All rights reserved.Legal|Privacy policy|Modern Slavery Act Transparency Statement|Sitemap|About US| Contact US: help@patsnap.com