Lithium manganate production method
A production method and technology of lithium manganate, applied in the direction of manganate/permanganate, electrical components, battery electrodes, etc., can solve the problem of increased kiln heat preservation power, increased kiln heat loss, waste of energy and resources and other problems, to achieve the effects of shortening the firing time, increasing production capacity and reducing heat loss
- Summary
- Abstract
- Description
- Claims
- Application Information
AI Technical Summary
Problems solved by technology
Method used
Examples
Embodiment 1
[0023] First, take 87kg of electrolytic manganese dioxide, 45.8kg of manganese tetraoxide, and 33.3kg of lithium carbonate as raw materials, and mix them with a molar ratio of Mn:Mn:Li of 5:3:4.5, and dry mix to obtain a fully mixed and uniform After that, the mixed raw materials are heated to 500°C and kept for 2 hours; the pre-fired materials are pressed into blocks and stacked for firing; the firing temperature is 800°C, kept for 5 hours, and then cooled naturally to complete the sintering process , that is, the product is obtained.
Embodiment 2
[0025] First, take 87kg of electrolytic manganese dioxide, 45.8kg of trimanganese tetraoxide, and 37kg of lithium carbonate as raw materials, mix them with a molar ratio of Mn:Mn:Li of 5:3:5, and add 3.4kg of alumina Powder, to obtain fully mixed and uniform raw materials by dry mixing; then heat the mixed raw materials to 550°C and keep them warm for 2 hours; press the pre-fired materials into blocks and stack them for firing; the firing temperature is 850°C and keep warm for 3 hours Hours, and then lower the temperature naturally to complete the sintering process and obtain the product.
Embodiment 3
[0027] First, take 87kg of electrolytic manganese dioxide, 45.8kg of trimanganese tetraoxide, and 37kg of lithium carbonate as raw materials, mix them with a molar ratio of Mn:Mn:Li of 5:3:5, and add 1.7kg of cobalt oxide Powder, to obtain fully mixed and uniform raw materials by dry mixing; then heat the mixed raw materials to 550 ° C and keep them warm for 2 hours; press the pre-fired materials into blocks and stack them for firing; the firing temperature is 900 ° C and keep them warm for 3 hours. Hours, and then lower the temperature naturally to complete the sintering process and obtain the product.
PUM
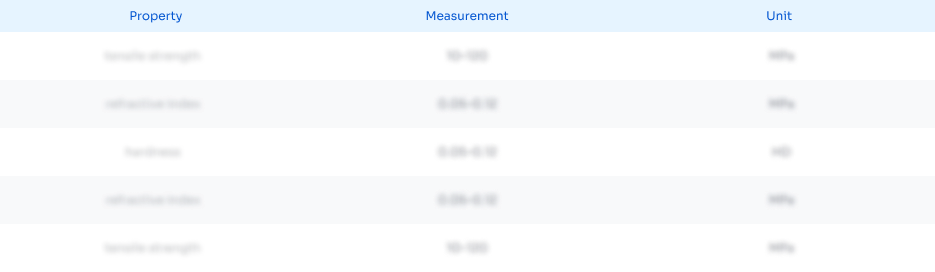
Abstract
Description
Claims
Application Information

- R&D
- Intellectual Property
- Life Sciences
- Materials
- Tech Scout
- Unparalleled Data Quality
- Higher Quality Content
- 60% Fewer Hallucinations
Browse by: Latest US Patents, China's latest patents, Technical Efficacy Thesaurus, Application Domain, Technology Topic, Popular Technical Reports.
© 2025 PatSnap. All rights reserved.Legal|Privacy policy|Modern Slavery Act Transparency Statement|Sitemap|About US| Contact US: help@patsnap.com