Sleeve type double-hearth shaft kiln
A double-chamber vertical kiln and sleeve-type technology, which is applied in the field of bulk material roasting kilns, can solve the difficulty of installing cantilever spray guns and spray gun protective covers, uneven heat distribution between the center and the periphery, and hinder the large-scale development of vertical kilns and other problems, to achieve the effect of improving uneven heat distribution, good product quality, and convenient installation
- Summary
- Abstract
- Description
- Claims
- Application Information
AI Technical Summary
Problems solved by technology
Method used
Image
Examples
Embodiment Construction
[0019] The specific implementation manners of the present invention will be further described in detail below in conjunction with the accompanying drawings.
[0020] See figure 1 , figure 2 , is a schematic diagram of the structure of the embodiment of the sleeve-type double-chamber shaft kiln of the present invention, including two symmetrical kiln chambers 1 and fuel spray guns 2, the inside of the kiln chamber 1 is respectively a preheating zone, a roasting zone and a cooling zone from bottom to top, and two The kiln chamber 1 is connected through the connecting channel 3 at the intersection of the calcination zone and the cooling zone. The outlet of the fuel spray gun 2 is set in the cross-sectional area of the kiln chamber 1. The centers of the two kiln chambers 1 are respectively provided with inner sleeves 4, and the inner sleeves The lower end of 4 is fixed on the discharge device 5 at the bottom of the kiln chamber, the upper end of the inner sleeve 4 is hinged wi...
PUM
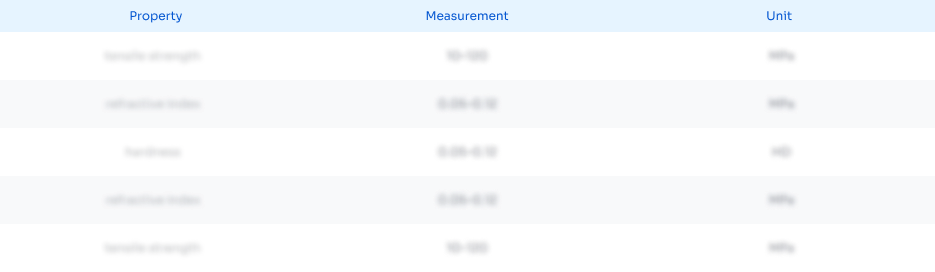
Abstract
Description
Claims
Application Information

- R&D
- Intellectual Property
- Life Sciences
- Materials
- Tech Scout
- Unparalleled Data Quality
- Higher Quality Content
- 60% Fewer Hallucinations
Browse by: Latest US Patents, China's latest patents, Technical Efficacy Thesaurus, Application Domain, Technology Topic, Popular Technical Reports.
© 2025 PatSnap. All rights reserved.Legal|Privacy policy|Modern Slavery Act Transparency Statement|Sitemap|About US| Contact US: help@patsnap.com