Spinel-supported catalyst for dry reforming of coke oven gas and preparation method thereof
A supported catalyst and coke oven gas technology, which is applied in chemical instruments and methods, physical/chemical process catalysts, metal/metal oxide/metal hydroxide catalysts, etc., can solve problems that do not involve catalyst stability, etc.
- Summary
- Abstract
- Description
- Claims
- Application Information
AI Technical Summary
Problems solved by technology
Method used
Image
Examples
Embodiment 1
[0023] 120 mmol Al(NO 3 ) 3 9H 2 O, 60 mmol Mg(NO 3 ) 2 ·6H 2 O and 2.76 mol urea were dissolved in a container filled with a certain amount of deionized water, and 50 g of polyethylene oxide-polypropylene oxide-polyethylene oxide triblock copolymer (P123, Ma=5800) was taken Dissolve in another container with a certain amount of deionized water. After P123 is dissolved, mix the samples in the two containers evenly and heat to 105~120 through an oil bath. o C, with vigorous stirring for 36 hours. The resulting precipitate was suction-filtered, washed twice with deionized water, and then washed at 120 o C dried overnight, and then the dried sample at 650 o C roasting for 8 hours, and finally grinding the obtained solid into powder, taking spinel powder within the range of 100-200 mesh as a carrier.
[0024] Take 4.259 mmol Ni(NO 3 ) 2 ·6H 2 O was made into a solution with deionized water, and 5 g of the above-mentioned prepared carrier was added to it, and after being...
Embodiment 2
[0026] First, the spinel powder carrier was prepared by the same method as in the above-mentioned Example 1.
[0027] Take 6.791 mmol Co(NO 3 ) 2 ·6H 2 O was made into a solution with deionized water, and 5 g of the above-mentioned prepared carrier was added to it, and after being fully stirred, it was placed in an ultrasonic water tank for ultrasonic immersion for 1 hour, followed by immersion at room temperature for 48 hours, at 100±10 o C stirring continuously until dry, and at 120 o C after drying for 5 hours, then at 850 o C roasting for 5 hours, crush the obtained solid into powder, use a mold with a diameter of 1.5 cm, shape it under a pressure of 10 kN (keep the pressure for 1 minute), crush it, sieve it, and take the range of 20 to 40 mesh as Catalyst, the catalyst is recorded as Co / MgAl 2 o 4 .
Embodiment 3
[0029] First, the spinel powder carrier was prepared by the same method as in the above-mentioned Example 1.
[0030] Take 3.396 mmol Ni(NO 3 ) 2 ·6H 2 O, 0.469 mmol PdCl 2 Make a solution with deionized water, add 5 g of the above prepared carrier to it, stir thoroughly, put it into an ultrasonic water tank for ultrasonic immersion for 1 hour, then immerse at room temperature for 24 hours, at 100±10 o C stirring continuously until dry, and at 110 o C dried for 5 hours, then at 800 o C roasting for 2 hours, crush the obtained solid into powder, use a mold with a diameter of 1.5 cm, shape it under a pressure of 15 kN (keep the pressure for 1 minute), crush it, sieve it, and take the range of 20 to 40 mesh as Catalyst, this catalyst is recorded as Ni-Pd / MgAl 2 o 4 .
PUM
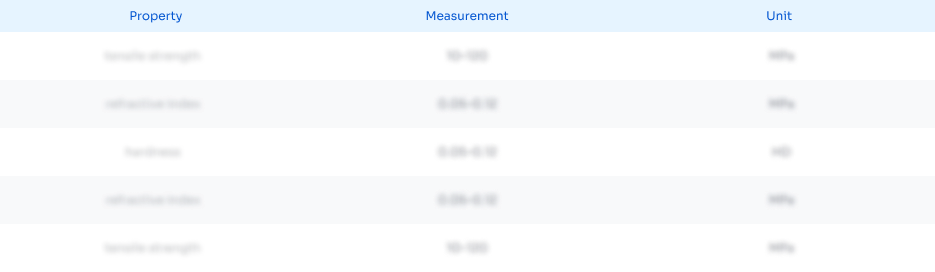
Abstract
Description
Claims
Application Information

- R&D
- Intellectual Property
- Life Sciences
- Materials
- Tech Scout
- Unparalleled Data Quality
- Higher Quality Content
- 60% Fewer Hallucinations
Browse by: Latest US Patents, China's latest patents, Technical Efficacy Thesaurus, Application Domain, Technology Topic, Popular Technical Reports.
© 2025 PatSnap. All rights reserved.Legal|Privacy policy|Modern Slavery Act Transparency Statement|Sitemap|About US| Contact US: help@patsnap.com