Large vacuum hot-pressing furnace
A vacuum hot-pressing furnace, a large-scale technology, used in non-electric welding equipment, welding equipment, metal processing equipment, etc., can solve the problems of hydraulic displacement accuracy and low temperature control accuracy, and improve the temperature uniformity and temperature control accuracy of samples. Ensure temperature uniformity and achieve the effect of precise control
- Summary
- Abstract
- Description
- Claims
- Application Information
AI Technical Summary
Problems solved by technology
Method used
Image
Examples
Embodiment 1
[0018] Such as figure 1 and 2 As shown, the technical solution adopted in the present invention is: a large-scale vacuum hot-press furnace, including a furnace body skeleton 1, a vacuum chamber 8, a vacuum obtaining system 10, a hydraulic system 9, a heating chamber 11, and six surfaces inserted into the vacuum chamber 8 The heating electrode 14, the thermocouple 16 inserted into the six sides of the heating chamber 11, the furnace frame and the hydraulic system 9 installed on its upper end, the molybdenum pressure rod 4 connected to the hydraulic system and the molybdenum flange 13 connected to the molybdenum pressure rod 4 , the upper molybdenum indenter 5 connected with the molybdenum flange 13, the lower molybdenum indenter sample stage 6 installed in the heating chamber 11 and four molybdenum support columns 7,18,20,21 in contact with it; and the molybdenum support column 7, 18, 20, 21 are in contact with heat-insulating ceramic sheets 17; four stainless steel columns 12...
Embodiment 2
[0021] According to implementation 1 operation steps, with P20 mold steel as material, adopt a kind of large-scale vacuum hot-press furnace of the present invention to manufacture the automobile fog lamp sight ring injection mold that contains conformal flow channel (φ 3mm), such as image 3 shown. The maximum working distance of the upper molybdenum indenter 5 and the lower molybdenum indenter 6 is 210mm; when the heating chamber 11 is heated to 1000°C, the hydraulic system 9 is started to pressurize the workpiece, the pressure is 120 tons, the hydraulic stroke is 0.035mm, heat preservation and pressure maintaining 1 hour. Figure 4 It is the metallographic micrograph of the welding surface. It can be seen from the picture that it is difficult to find the welding line under the condition of magnification of 50 times. By using the injection mold with conformal runner inside, the injection cooling time can be reduced to 18 seconds compared with the traditional injection mold, ...
Embodiment 3
[0023] By implementing 1 operation step, using P20 mold steel as material, adopting a kind of large-scale vacuum hot pressing furnace of the present invention to manufacture a large-scale injection mold with a height of 300mm. Replace the four molybdenum columns 7, 18, 20, 21 so that the maximum working distance between the upper molybdenum indenter 5 and the lower molybdenum indenter sample table 6 is 310mm; when the heating chamber 11 is heated to 1000°C, start the hydraulic system 9 to process the workpiece Pressure, the pressure is 180 tons, the hydraulic stroke is 0.05mm, and the heat preservation and pressure are maintained for 1.5 hours.
PUM
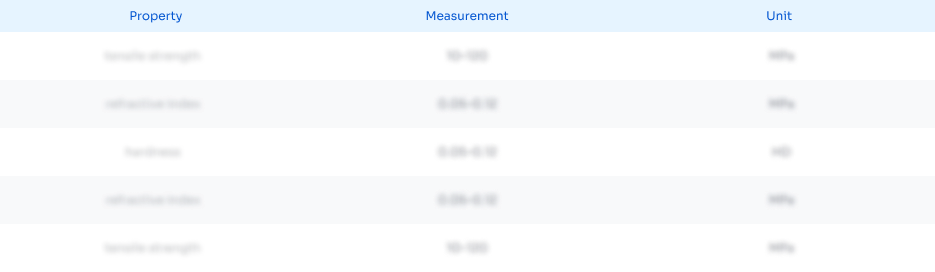
Abstract
Description
Claims
Application Information

- Generate Ideas
- Intellectual Property
- Life Sciences
- Materials
- Tech Scout
- Unparalleled Data Quality
- Higher Quality Content
- 60% Fewer Hallucinations
Browse by: Latest US Patents, China's latest patents, Technical Efficacy Thesaurus, Application Domain, Technology Topic, Popular Technical Reports.
© 2025 PatSnap. All rights reserved.Legal|Privacy policy|Modern Slavery Act Transparency Statement|Sitemap|About US| Contact US: help@patsnap.com