Machine tool spindle device of numerically-controlled gear milling machine for spiral bevel gear
A technology of spiral bevel gears and tool spindles, which is applied in the direction of manufacturing tools, metal processing machinery parts, large fixed members, etc., can solve the problems of loss of transmission accuracy and transmission efficiency, limitation of the movement speed of tool spindles, affecting the machining accuracy of bevel gears, etc. Achieve the effect of improving machining accuracy and smoothness, improving machining accuracy, improving transmission accuracy and transmission stability
- Summary
- Abstract
- Description
- Claims
- Application Information
AI Technical Summary
Problems solved by technology
Method used
Image
Examples
Embodiment Construction
[0013] In order to further understand the invention content, characteristics and effects of the present invention, the following examples are given, and detailed descriptions are as follows in conjunction with the accompanying drawings:
[0014] see figure 1 , CNC spiral bevel gear milling machine tool spindle device, including a spindle box 11 and a tool spindle 14 arranged in the spindle box. A torque motor stator 2 and a torque motor rotor 3 are fixed in the spindle housing, and the torque motor rotor 3 is fixed on the taper sleeve 1 located in the spindle housing, and is connected with the tool spindle through a flat key. The tool spindle is supported and fixed in the main shaft housing 11 and the casing back cover 27 by the front bearing 12, the rear bearing 10 and the auxiliary bearing. Cover 25. One end of the tool spindle is sealed by the front end cover 13, the other end of the tool spindle is equipped with an encoder 20 through a sleeve 29 and a third lock nut 28, ...
PUM
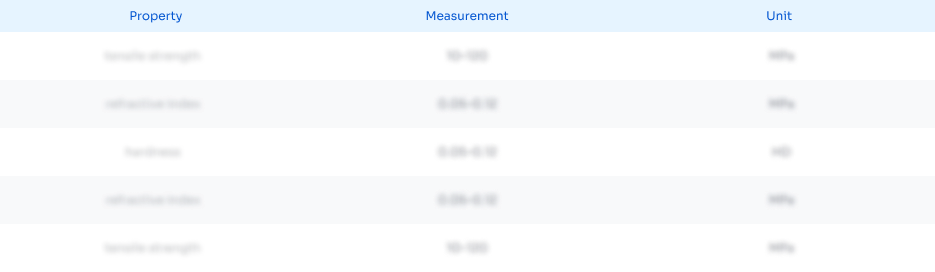
Abstract
Description
Claims
Application Information

- R&D Engineer
- R&D Manager
- IP Professional
- Industry Leading Data Capabilities
- Powerful AI technology
- Patent DNA Extraction
Browse by: Latest US Patents, China's latest patents, Technical Efficacy Thesaurus, Application Domain, Technology Topic, Popular Technical Reports.
© 2024 PatSnap. All rights reserved.Legal|Privacy policy|Modern Slavery Act Transparency Statement|Sitemap|About US| Contact US: help@patsnap.com