Furnace building method for rotary kiln tube body inner liner
A rotary kiln and cylinder body technology, applied in the field of rotary kiln, can solve the problems of easy crushing of heat-insulating fiberboard, affecting the service life of the cylinder, large heat dissipation of the cylinder, etc., to solve the problems of easy damage and pulverization, and reduce the cost of the furnace building process Low, the effect of reducing process energy consumption
- Summary
- Abstract
- Description
- Claims
- Application Information
AI Technical Summary
Problems solved by technology
Method used
Image
Examples
Embodiment Construction
[0049]The present invention will be further described in detail below in conjunction with the accompanying drawings and specific preferred embodiments.
[0050] A method for lining a rotary kiln shell of the present invention, the steps are:
[0051] (1) Clean the inner surface of the rotary kiln shell 1, and draw several circles along the diameter direction of the rotary kiln shell 1 to divide the rotary kiln shell 1 into several sections; Draw several parallel straight lines on the body 1, and the above-mentioned sections of cylinder are divided into several bars. In the above step (1), the actual operation is as follows: at the beginning of the furnace construction, the rotary kiln shell 1 is laid out along the radial direction to divide the shell into several sections, and the length of each section is 15m to 30m; Divide the cylinder into multiple strip-shaped areas, each area has an angle of 5° to 15°. The number of constructions along the circumferential direction is 3...
PUM
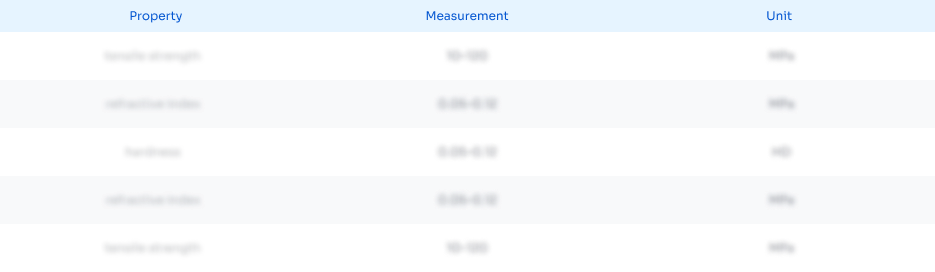
Abstract
Description
Claims
Application Information

- Generate Ideas
- Intellectual Property
- Life Sciences
- Materials
- Tech Scout
- Unparalleled Data Quality
- Higher Quality Content
- 60% Fewer Hallucinations
Browse by: Latest US Patents, China's latest patents, Technical Efficacy Thesaurus, Application Domain, Technology Topic, Popular Technical Reports.
© 2025 PatSnap. All rights reserved.Legal|Privacy policy|Modern Slavery Act Transparency Statement|Sitemap|About US| Contact US: help@patsnap.com