Clean and environment-friendly comprehensive novel recycling process by virtue of high-indium high-iron zinc concentrate
A high-iron zinc and zinc concentrate technology, which is applied in the field of comprehensive recovery of zinc, indium and iron in hydrometallurgical integrated innovative technology, can solve the problem of low direct yield of zinc smelting, difficult recovery of sulfide ore and the consumption of elemental sulfur and zinc concentrate Large and other problems, to achieve the effect of complete separation, efficient separation, and high metal recovery rate
- Summary
- Abstract
- Description
- Claims
- Application Information
AI Technical Summary
Problems solved by technology
Method used
Image
Examples
Embodiment 1
[0047] Main components of zinc calcine hot acid leaching solution (g / L): Zn104.52, In0.15, Fe 总 20.5, H 2 SO 4 51.4, heat up the hot acid leaching solution to 85°C, add zinc concentrate with a particle size below 0.074mm accounting for 90% as a reducing agent, and the amount of reducing agent added is Fe 3+ The theoretical amount is reduced by 1.05 times, and the reduction time is 3 hours. Fe in the hot acid leaching solution after reduction 3+ 1.36g / L, the final acid concentration was 38.2g / L.
[0048] Add limestone to the hot acid leach solution after reduction, the mass of limestone added is 85% of the theoretical amount, the neutralization time is 60min, the neutralization process temperature is controlled at 60°C, the neutralization final acid concentration is 10g / L, and the neutralization slag contains In0. 0011%, In loss is less than 0.15%.
[0049] Add zinc oxide to the solution after neutralization, the mass of zinc oxide added is 120% of the theoretical amount, t...
Embodiment 2
[0053] Main components of zinc calcine hot acid leaching solution (g / L): Zn101.8, In0.18, Fe 总 28.4, H 2 SO 4 45.8, the temperature of the hot acid leaching solution was raised to 95°C, and SO was added 2 As a reducing agent, the amount of reducing agent added is Fe 3+ The theoretical amount is reduced by 1.75 times, and the reduction time is 3 hours. Fe in the hot acid leaching solution after reduction 3+ 1.76g / L, the final acid concentration was 50.2g / L.
[0054] Limestone was added to the hot acid leaching solution after reduction, the mass of limestone added was 70% of the theoretical amount, the neutralization time was 60min, the neutralization process temperature was controlled at 60°C, the neutralization final acid concentration was 15g / L, and the neutralization slag contained In0. 0003%, In loss is less than 0.07%.
[0055] Add zinc powder to the neutralized solution, the mass of zinc powder added is 200% of the theoretical amount, the reaction temperature is 60°C...
PUM
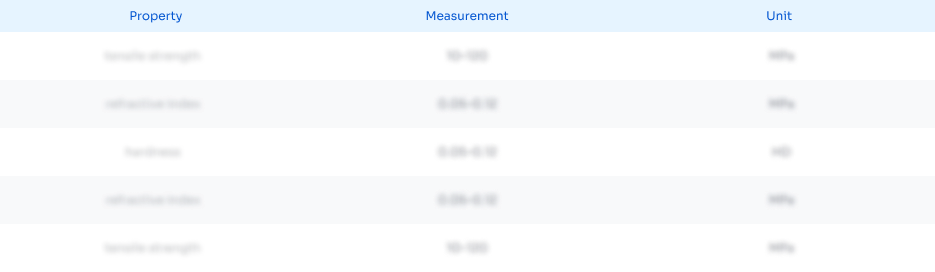
Abstract
Description
Claims
Application Information

- R&D Engineer
- R&D Manager
- IP Professional
- Industry Leading Data Capabilities
- Powerful AI technology
- Patent DNA Extraction
Browse by: Latest US Patents, China's latest patents, Technical Efficacy Thesaurus, Application Domain, Technology Topic, Popular Technical Reports.
© 2024 PatSnap. All rights reserved.Legal|Privacy policy|Modern Slavery Act Transparency Statement|Sitemap|About US| Contact US: help@patsnap.com