Flame-retardant anti-electric leakage high-performance environment-friendly PBT (polybutylene terephthalate) material and preparation method thereof
A high-performance, leakage-resistant technology, applied in the field of PBT materials and their preparation, can solve the problems of dependence on imports and inability to produce halogen-free, environmentally friendly, flame-retardant, high-leakage-resistant reinforced PBT materials, etc., to improve compatibility and excellent mechanical properties. , the effect of high thermal stability
- Summary
- Abstract
- Description
- Claims
- Application Information
AI Technical Summary
Problems solved by technology
Method used
Examples
Embodiment 1
[0018] A flame-retardant, leakage-resistant, high-performance and environmentally friendly PBT material, its components are proportioned by mass percentage: PBT 50%, phosphinate flame retardant CJ1002 18%, calcium oxide 1%, alkali-free glass fiber 25%, Composite antioxidant JC-1215 0.5%, EVA wax 0.5%, glycidyl methacrylate graft POE 4%, silane coupling agent 1%.
[0019] Preparation method: (1) Mix the above components in proportion; (2) Dry PBT at 120°C-140°C for 4-6 hours, phosphinate flame retardant CJ1002 and alkali-free glass fiber at 100°C- Dry at 120°C for 30 to 45 minutes; (3) Put the dried PBT, phosphinate flame retardant CJ1002 and alkali-free glass fiber in a high-speed mixer, and at the same time add calcium oxide, composite antioxidant JC-1215, EVA wax, glycidyl methacrylate grafted POE and silane coupling agent are placed in the same high-speed mixer and mixed evenly through the high-speed mixer; (4) Add the above-mentioned mixture to the twin-screw extruder, and...
Embodiment 2
[0021] A flame-retardant, leakage-resistant, high-performance and environmentally-friendly PBT material, its components are: PBT 60%, phosphinate flame retardant CJ1002 18%, calcium oxide 2%, alkali-free glass fiber 18%, Hindered phenol antioxidant KY-1076 0.3%, AClyn low molecular weight ionomer 0.5%, low density polyethylene 1%, silane coupling agent 0.2%.
[0022] Preparation method: (1) Mix the above components in proportion; (2) Dry PBT at 120°C-140°C for 4-6 hours, phosphinate flame retardant CJ1002 and alkali-free glass fiber at 100°C- Dry at 120°C for 30-45 minutes; (3) Put the dried PBT, phosphinate flame retardant CJ1002 and alkali-free glass fiber in a high-speed mixer, and at the same time add calcium oxide, hindered phenol antioxidant KY-1076 , AClyn low-molecular-weight ionomer, low-density polyethylene and silane coupling agent are placed in the same high-speed mixer, and mixed evenly through the high-speed mixer; (4) Add the above-mentioned mixture to the twin-...
Embodiment 3
[0024] A flame-retardant, leakage-resistant, high-performance and environmentally-friendly PBT material, its components are: PBT 45%, phosphinate flame retardant CJ1002 20%, calcium oxide 1%, alkali-free glass fiber 30%, Composite antioxidant JC-1215 0.5%, calcium stearate 0.5%, ethylene-butyl acrylate-glycidyl ester terpolymer 2%, silane coupling agent 1%.
[0025] Preparation method: (1) Mix the above components in proportion; (2) Dry PBT at 120°C-140°C for 4-6 hours, phosphinate flame retardant CJ1002 and alkali-free glass fiber at 100°C- Dry at 120°C for 30 to 45 minutes; (3) Put the dried PBT, phosphinate flame retardant CJ1002 and alkali-free glass fiber in a high-speed mixer, and at the same time add calcium oxide, composite antioxidant JC-1215, Calcium stearate, ethylene-butyl acrylate-glycidyl ester terpolymer and silane coupling agent are placed in the same high-speed mixer and mixed evenly by the high-speed mixer; (4) Add the above-mentioned mixture to the twin-scre...
PUM
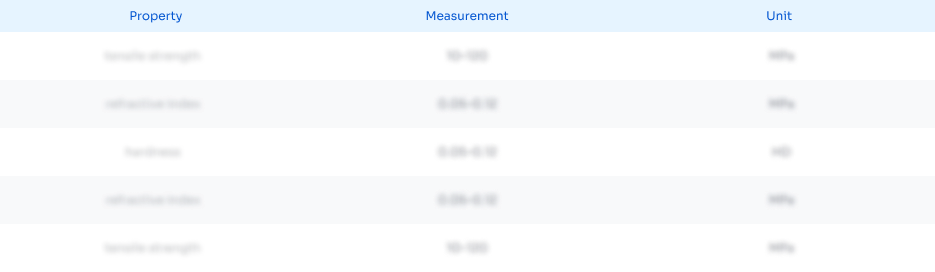
Abstract
Description
Claims
Application Information

- Generate Ideas
- Intellectual Property
- Life Sciences
- Materials
- Tech Scout
- Unparalleled Data Quality
- Higher Quality Content
- 60% Fewer Hallucinations
Browse by: Latest US Patents, China's latest patents, Technical Efficacy Thesaurus, Application Domain, Technology Topic, Popular Technical Reports.
© 2025 PatSnap. All rights reserved.Legal|Privacy policy|Modern Slavery Act Transparency Statement|Sitemap|About US| Contact US: help@patsnap.com