Method for preparing tubular ceramic membrane for oil-water separation
A technology of oil-water separation and ceramic membrane, which is applied in the chemical field and can solve the problem of low filtration flux
- Summary
- Abstract
- Description
- Claims
- Application Information
AI Technical Summary
Problems solved by technology
Method used
Examples
Embodiment 1
[0011] Three aluminum oxide ceramic membrane tubes with an initial bubble point of 0.52Mpa were respectively selected as substrates; polytetrafluoroethylene membrane-making liquid was prepared in a pure water system, and the mass percent concentration of polytetrafluoroethylene in the membrane-making liquid was controlled at 3.3 %, completely dissolved and left to stand for 12 hours, under stirring, slowly add porogen and special binder, control the final mass percentage concentration of porogen to 0.04%, and the final mass percentage concentration of binder to 0.01% ; In this process, KCL is used as porogen, and aluminate is used as binder. During the coating process, the flow rate of the membrane-forming liquid is controlled to 1.5 m / s, the pressure difference between the inlet and outlet of the membrane tube is 0.12Mpa, and the coating time is 35s; the coated ceramic membrane tube is dried in an oven, and the temperature of the oven is controlled at 120°C. Time 8h. The dri...
Embodiment 2
[0014] Three aluminum oxide ceramic membrane tubes with an initial bubble point of 0.52Mpa were respectively selected as substrates; polyvinylidene fluoride membrane-making liquid was prepared in a pure water system, and the mass percentage of polyvinylidene fluoride membrane-making liquid in the membrane-making liquid was Control the concentration at 5.6%, let it stand for 12 hours after completely dissolving, and slowly add porogen and binder under stirring, control the final mass percentage concentration of porogen to 0.07%, and the final mass percentage of binder The concentration is 0.02%; among them, KCL is used as the porogen, and phosphate is used as the binder. During the coating process, the flow rate of the membrane-forming liquid is controlled to 1 m / s, the pressure difference between the inlet and outlet of the membrane tube is 0.12Mpa, and the coating time is 20s; the coated ceramic membrane tube is dried in an oven, and the temperature of the oven is controlled a...
Embodiment 3
[0017] Three aluminum oxide ceramic membrane tubes with an initial bubble point of 0.58Mpa were respectively selected as substrates; polyvinylidene fluoride film-making liquid was prepared in a pure water system, and the mass percentage concentration of polyvinylidene fluoride in the film-making liquid was controlled At 7.8%, let it stand for 12 hours after completely dissolving, and slowly add porogen and binder under stirring, control the final mass percentage concentration of porogen to 0.08%, and the final mass percentage concentration of binder The concentration is 0.03%; NaCl is used as the porogen, and borate is used as the binder. During the coating process, the flow rate of the membrane-forming liquid was controlled to be 1.8 m / s, the pressure difference between the inlet and outlet of the membrane tube was 0.16Mpa, and the coating time was 45s; the coated ceramic membrane tube was dried in an oven, and the temperature of the oven was controlled at 1.5°C. Time 12h. T...
PUM
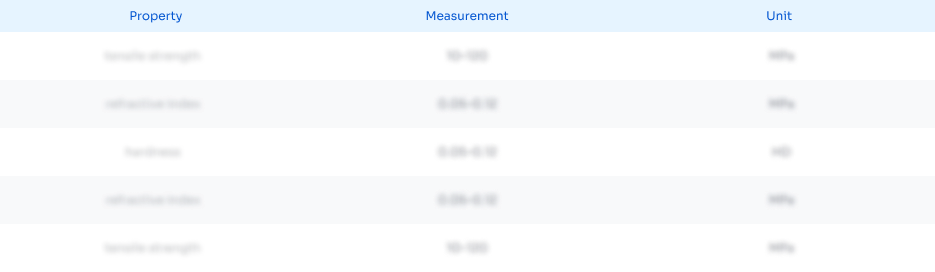
Abstract
Description
Claims
Application Information

- Generate Ideas
- Intellectual Property
- Life Sciences
- Materials
- Tech Scout
- Unparalleled Data Quality
- Higher Quality Content
- 60% Fewer Hallucinations
Browse by: Latest US Patents, China's latest patents, Technical Efficacy Thesaurus, Application Domain, Technology Topic, Popular Technical Reports.
© 2025 PatSnap. All rights reserved.Legal|Privacy policy|Modern Slavery Act Transparency Statement|Sitemap|About US| Contact US: help@patsnap.com