Method for recovering copper and nickel from nickel-iron-copper alloy waste
A nickel-iron-copper and copper recovery technology, which is applied in the field of comprehensive utilization of resources, can solve the problems of poor economic performance and low utilization rate, and achieve the effects of low production cost, simple operation, and remarkable energy-saving effect of the process
- Summary
- Abstract
- Description
- Claims
- Application Information
AI Technical Summary
Problems solved by technology
Method used
Image
Examples
Embodiment 1
[0024] Such as figure 1 Shown, this method for reclaiming copper, nickel from nickel-iron-copper alloy scrap, its concrete steps are as follows:
[0025] (1) Oxidation and iron removal: first, heat up the nickel-iron-copper alloy scrap to 1500°C to obtain molten nickel-iron-copper alloy scrap, then add slagging agent to the molten nickel-iron-copper alloy scrap and spray oxidizing gas to maintain this temperature After reacting for 10 minutes, molten metal and slag are obtained. The nickel-iron-copper alloy waste includes the following components in mass percentage: Fe0.5%, Cu80%, Ni19.5%; the slagging agent is SiO 2 , the amount added is 0.5 times the mass of iron in the nickel-iron-copper alloy; the oxidizing gas is air, and the injection pressure is 0.01MPa;
[0026] (2) One-stage electrolytic refining to recover copper: cast the molten metal obtained in step (1) into a soluble anode, then use the soluble anode plate as the anode, the stainless steel plate as the cathode, ...
Embodiment 2
[0034] Such as figure 1 Shown, this method for reclaiming copper, nickel from nickel-iron-copper alloy scrap, its concrete steps are as follows:
[0035] (1) Oxidation and iron removal: firstly, the nickel-iron-copper alloy scrap is heated to 1650°C to obtain molten nickel-iron-copper alloy scrap, then a slagging agent is added to the molten nickel-iron-copper alloy scrap and oxidizing gas is sprayed to maintain the temperature After reacting for 120 minutes, molten metal and slag were obtained, in which the nickel-iron-copper alloy scrap included the following components in mass percentage: Fe20%, Cu60%, Ni20%; the slagging agent was SiO with a mass ratio of 1:1 2 Mixed with blast furnace slag, the amount added is 2.5 times the mass of iron in the nickel-iron-copper alloy; the oxidizing gas is oxygen-enriched air, and the injection pressure is 0.8MPa;
[0036] (2) One-stage electrolytic refining to recover copper: cast the molten metal obtained in step (1) into a soluble ano...
Embodiment 3
[0044] Such as figure 1 Shown, this method for reclaiming copper, nickel from nickel-iron-copper alloy scrap, its concrete steps are as follows:
[0045] (1) Oxidation and iron removal: firstly, the nickel-iron-copper alloy scrap is heated to 1600°C to obtain molten nickel-iron-copper alloy scrap, then a slagging agent is added to the molten nickel-iron-copper alloy scrap and oxidizing gas is sprayed to maintain the temperature After reacting for 80 minutes, molten metal and slag were obtained, wherein the nickel-iron-copper alloy waste material included the following components in mass percent: Fe19%, Cu78%, Ni3%; the slagging agent was blast furnace slag, and the amount added was the mass of iron in the nickel-iron-copper alloy 1.5 times; the oxidizing gas is oxygen, and the injection pressure is 0.5MPa;
[0046] (2) One-stage electrolytic refining to recover copper: cast the molten metal obtained in step (1) into a soluble anode, then use the soluble anode plate as the ano...
PUM
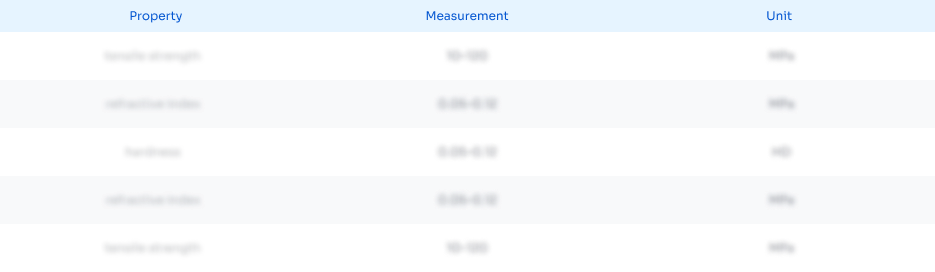
Abstract
Description
Claims
Application Information

- Generate Ideas
- Intellectual Property
- Life Sciences
- Materials
- Tech Scout
- Unparalleled Data Quality
- Higher Quality Content
- 60% Fewer Hallucinations
Browse by: Latest US Patents, China's latest patents, Technical Efficacy Thesaurus, Application Domain, Technology Topic, Popular Technical Reports.
© 2025 PatSnap. All rights reserved.Legal|Privacy policy|Modern Slavery Act Transparency Statement|Sitemap|About US| Contact US: help@patsnap.com