Polyethylene foam material prepared by utilizing recycled foam material and production method thereof
A technology of polyethylene foaming and foaming materials, applied in the field of polyethylene foaming materials, can solve problems such as pollution, poor product quality, waste of resources and the environment, and achieve the effects of reducing production costs, consistent internal structure, and protecting the environment
- Summary
- Abstract
- Description
- Claims
- Application Information
AI Technical Summary
Problems solved by technology
Method used
Image
Examples
Embodiment 1
[0023] A polyethylene foam material prepared by foaming recycled materials, comprising the following components in order by weight: 50 kg of cross-linked polyethylene foam material waste, 16 kg of composite filler, 0.5 kg of compound cross-linking agent, compound hair Foaming agent 3.2kg, foaming aid 0.8kg.
[0024] The composite filler is composed of 12.8kg of talc powder and 3.2kg of nano-calcium carbonate particles.
[0025] The compounded cross-linking agent is compounded by 0.375kg of dicumyl peroxide and 0.125kg of 2,5-di-tert-butylperoxy-2,5-dimethylhexane.
[0026] The compound blowing agent is made by mixing 2.45kg of azodicarbonamide, 0.5kg of sodium bicarbonate and 0.25kg of sodium citrate.
[0027] The foaming aid is formed by mixing 0.1kg of zinc oxide, 0.3kg of zinc carbonate and 0.4kg of zinc stearate.
[0028] A kind of production method that the polyethylene foam material that utilizes foaming regrind to prepare as above-mentioned comprises the following ste...
Embodiment 2
[0036] A polyethylene foam material prepared by foaming recycled materials, comprising the following components in parts by weight in turn: 80 kg of cross-linked polyethylene foam material waste, 25 kg of composite filler, 0.4 kg of compound cross-linking agent, compound hair Foaming agent 5kg, foaming aid 1kg.
[0037] The composite filler is composed of 20kg of talcum powder and 5kg of nano-calcium carbonate particles.
[0038] The compounded cross-linking agent is compounded by 0.3 kg of dicumyl peroxide and 0.1 kg of 2,5-di-tert-butyl peroxy-2,5-dimethylhexane.
[0039] The compound blowing agent is formed by mixing 3.84kg of azodicarbonamide, 0.76kg of sodium bicarbonate and 0.38kg of sodium citrate.
[0040] The foaming aid is formed by mixing 0.3kg of zinc oxide, 0.6kg of zinc carbonate and 0.1kg of zinc stearate.
[0041] A kind of production method that the polyethylene foam material that utilizes foaming regrind to prepare as above-mentioned comprises the following...
Embodiment 3
[0049] A polyethylene foam material prepared by foaming recycled materials, comprising the following components in parts by weight in turn: 100 kg of cross-linked polyethylene foam material waste, 20 kg of composite filler, 1.2 kg of compound cross-linking agent, compound hair Foaming agent 4kg, foaming aid 1.5kg.
[0050] The composite filler is made of 16kg of talcum powder and 4kg of nano-calcium carbonate particles.
[0051] The compound crosslinking agent is compounded by 0.9kg of dicumyl peroxide and 0.3kg of 2,5-di-tert-butyl peroxide-2,5-dimethylhexane.
[0052] The compound foaming agent is formed by mixing 3.07kg of azodicarbonamide, 0.62kg of sodium bicarbonate and 0.30kg of sodium citrate.
[0053] The foaming aid is formed by mixing 0.4kg of zinc oxide, 0.7kg of zinc carbonate and 0.4kg of zinc stearate.
[0054] A kind of production method that the polyethylene foam material that utilizes foaming regrind to prepare as above-mentioned comprises the following ste...
PUM
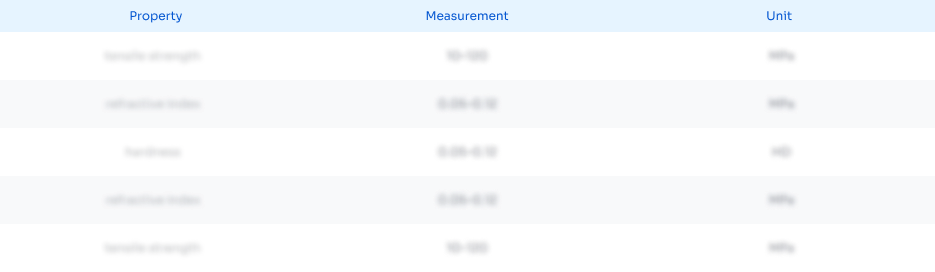
Abstract
Description
Claims
Application Information

- Generate Ideas
- Intellectual Property
- Life Sciences
- Materials
- Tech Scout
- Unparalleled Data Quality
- Higher Quality Content
- 60% Fewer Hallucinations
Browse by: Latest US Patents, China's latest patents, Technical Efficacy Thesaurus, Application Domain, Technology Topic, Popular Technical Reports.
© 2025 PatSnap. All rights reserved.Legal|Privacy policy|Modern Slavery Act Transparency Statement|Sitemap|About US| Contact US: help@patsnap.com