Preparation method of solventless ultraviolet-curing polyurethane for synthetic leather
A solvent-free, UV-light technology, applied in coatings, textiles, and papermaking, can solve solvent pollution and other problems, and achieve the effects of no pollution, convenient operation, and stable process
- Summary
- Abstract
- Description
- Claims
- Application Information
AI Technical Summary
Problems solved by technology
Method used
Examples
Embodiment 1
[0017] In parts by weight, put 100 parts of vacuum dehydrated liquid PPG2000 and 30 parts of toluene diisocyanate (TDI) into a nitrogen-protected reactor, stir and mix well, add 20 parts of acrylic acid-2-hydroxyl Propyl ester and 0.1 part of dibutyltin dilaurate were reacted at 75°C for 60 minutes, the resulting reaction system was cooled, and then 0.10 part of 2-hydroxy-methylphenylpropan-1-one was added and stirred evenly, that is Obtain solvent-free UV curing polyurethane.
Embodiment 2
[0019] In parts by weight, put 100 parts of LS707-55 (Shanxi Kaixire Technology Co., Ltd.) in liquid form after vacuum dehydration and 20 parts of isophorone diisocyanate (IPDI) into a reactor protected by nitrogen After stirring and mixing uniformly, add 15 parts of 2-hydroxypropyl methacrylate and 0.16 parts of stannous octoate, and then react at 80°C for 53 minutes, cool the resulting reaction system, and then add 0.05 parts of 2-formaldehyde -1-(4-Methylthiophenyl)-2-morpholin-1-acetone, stir evenly to obtain solvent-free UV-curable polyurethane.
Embodiment 3
[0021] In parts by weight, 20 parts of vacuum dehydrated liquid LS707-55 (Shanxi Kaixier Technology Co., Ltd.), 80 parts of vacuum dehydrated liquid PPG1000 and 40 parts of diphenylmethylene diisocyanate (MDI ) Put it into a nitrogen-protected reactor, stir and mix well, add 30 parts of 2-hydroxyethyl acrylate, 0.1 parts of stannous octoate and 0.2 parts of dibutyltin dilaurate, and then at 85°C After reacting for 40 minutes, the obtained reaction system is cooled, and then 0.15 parts of 1-hydroxycyclohexyl phenyl ketone is added and stirred uniformly to obtain solvent-free UV-curable polyurethane.
PUM
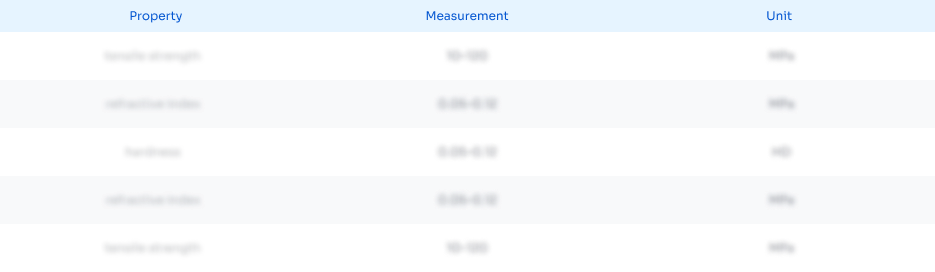
Abstract
Description
Claims
Application Information

- Generate Ideas
- Intellectual Property
- Life Sciences
- Materials
- Tech Scout
- Unparalleled Data Quality
- Higher Quality Content
- 60% Fewer Hallucinations
Browse by: Latest US Patents, China's latest patents, Technical Efficacy Thesaurus, Application Domain, Technology Topic, Popular Technical Reports.
© 2025 PatSnap. All rights reserved.Legal|Privacy policy|Modern Slavery Act Transparency Statement|Sitemap|About US| Contact US: help@patsnap.com